Domestic wood producers say that order backlogs and lead times have risen in recent months due to ongoing demand.
HIGH POINT — Domestic case goods manufacturers say they are seeing increases in their historically high backlogs, an indicator that business remains strong heading into the third and fourth quarters.
For retailers and consumers that likely will mean continued longer-than-normal wait times for finished goods for the balance of this year and heading into 2022 —and perhaps beyond.
It’s a situation many customers have become accustomed to, particularly with wood imports from Vietnam and Malaysia, which have experienced Covid-related shutdowns most of the summer. Yet domestic wood producers also are having trouble keeping up with the demand, too, making it a difficult balancing act when dealing with existing and new customers.
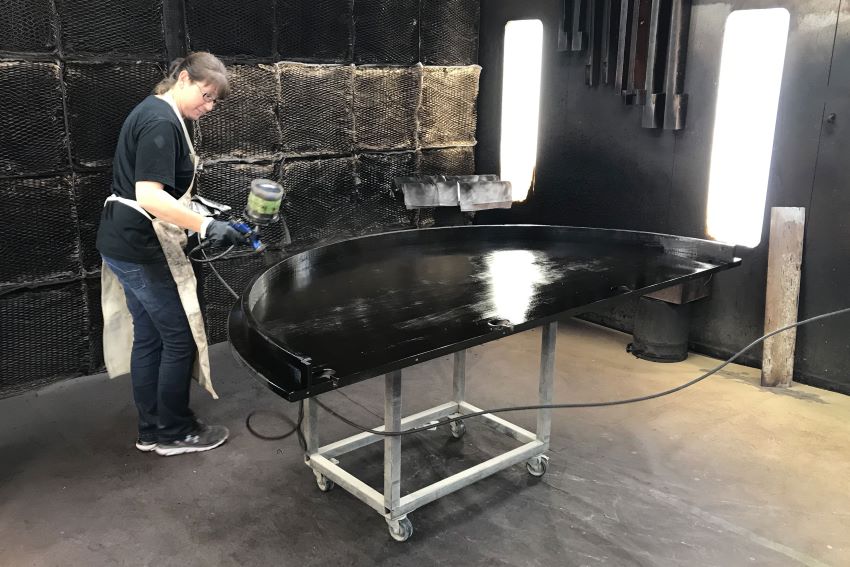
Kevin Kauffman, owner of solid wood furniture producer Simply Amish, said that lead times — which sources describe as the rough equivalent of backlogs — have been about 16-18 weeks for about two months. That’s up from roughly eight weeks in normal times — from the time of order to the time the product is ready to ship – and about 14 weeks in April.
Items in the company’s stocking program go out the door more quickly as they are shipped from inventory.
“We have increased production, but what we are putting out right now is a lot more than we are used to,” Kauffman told Home News Now. “We are adding equipment and people as fast as we can and where it makes sense, but it takes time to train people. I also have had some equipment on order that would normally be shipped right away, but it is taking a couple of months longer to get to us… They are having the same problems as we are having and can’t find extra help.”
The company, which also employs some outside contract manufacturers, is considering an expansion of its 110,000-square-foot plant in Arcola, Ill. But for now, it plans to stay around just under 60 workers in house, Kauffman said, noting the facility has reached its capacity. While he said the company is meeting its current demand by working longer hours and producing more product, he doesn’t expect lead times to get back to normal for another year.
“Demand would have to fall off for two months for us to get back to eight weeks,” he said, noting that the production has gotten to where it is not falling further behind the demand. “For a while, we were falling behind every week, but now we are able to keep up with the current demand. We are shipping the same amount we are taking in.”
Bedroom manufacturer Vaughan-Bassett Furniture has also seen its backlogs rise of late, said company President Doug Bassett. He said the company has had an $11 million, or five and a half week backlog for the past two months, double what it was around the end of May.
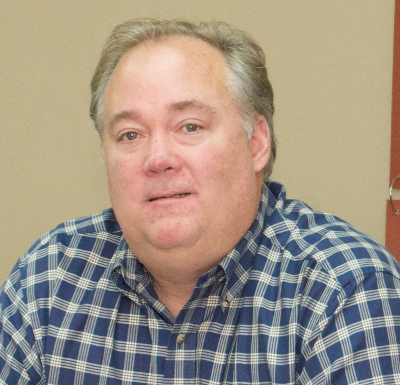
“Ours has not gotten better,” he said, noting that October was the biggest order month in over a decade, which he said was partly due to it being a five-week month. “We have steadily been receiving more orders than we are producing.”
“Our business is very strong and we are producing more furniture than we ever have,” he added. “We are doing all we can to keep up.”
As he told Home News Now previously, the company continues to address this by not taking on new accounts, instead focusing on existing customers.
He said the company also is helping dealers by shifting some from its warehouse to their warehouses which is allowing them to have stock further out on some top sellers.
In addition, he said that the company is attempting to communicate more accurate information to dealers on when goods will actually ship, which he noted also has gotten a little easier due to greater reliability from trucking companies compared to earlier in the year.
“We are able to very accurately say when a group is going to be ready to deliver,” he said, noting there could be exceptions of a day or two. “We stay close to that schedule.”
The company also has limited introductions of late and also pared down its line to focus on the strongest performers.
“We really only have nine or 10 active collections in our line,” Bassett said. “By keeping our line so short, we are able to get around our full schedule more quickly. And even though we have a backlog that is larger than ideal, we are able to get to every suite fairly quickly, multiple times a year. We will be very disciplined in how much product we offer dealers until we see that backlog moving down.”
He said the goal is to get back to a backlog of no more than two weeks. How soon that happens, though will be hard to predict as it’s affected by business moving forward.
Tim Copeland, president of solid wood furniture manufacturer Copeland Furniture, said he has no clear sense of when to expect lower backlogs.
Today, he said, the backlog is stronger than ever, at 23 weeks on made-to-order product, compared to the 16 weeks the company was experiencing during the first quarter and a more typical 6-8 weeks in normal times. By comparison, its Priority Shipment program of furniture built from a replenished parts inventory, is running at about 12-week lead times compared to a more typical two to four weeks.
“I think we are a long way from that,” Copeland said of getting back to more normal lead times.
“I don’t know when it will come down,” he added. “Lead times will depend on what the rate of orders is and what the rate of production is. We are going to do everything we can to raise the rate of production, but I can’t say what will happen with the rate of orders.”
The company also continues to add workers as it moves forward with an expansion into a neighboring building on its Bradford, Vt. campus.
“It has slowed down a great deal on account of the labor shortage,” he said, adding that the company has been able to hire about a dozen workers since mid-summer, bringing the total to 99. He said recent hires on the facilities staff have made it possible to begin moving more operations into the building, which is expected to begin production in January.
Fortunately, Copeland said, that the company is at the point where it is finally increasing production faster than orders are increasing. He also noted that orders also typically slow down some in November and December and that this year the company did not plan any special Black Friday promotions like it has done in previous years.
“We have such a backlog that we can use a little bit of softness for a couple of months,” Copeland said.
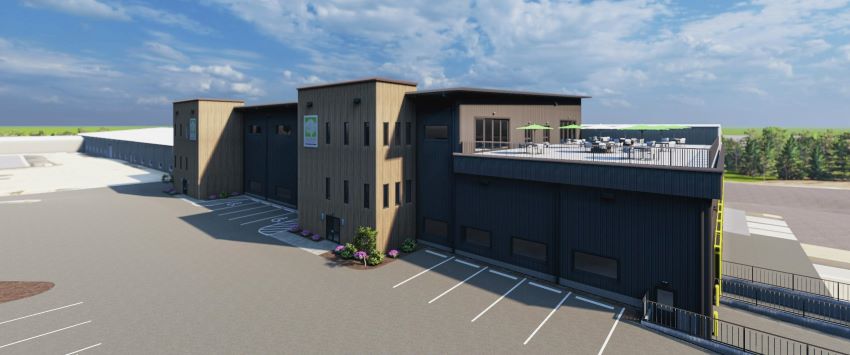
Solid wood furniture producer Palettes by Winesburg is also expanding its capacity, which should help manage a current backlog of 22 weeks, up from 20 weeks about a month ago.
“It is just incrementally growing,” said Sam Stoltzfus, sales manager. “Our order intake is higher than throughput.”
The company is doubling the size of its 88,000-square-foot plant in Dundee, Ohio, with half of the expansion expected to be completed by year end and the remainder by July 2022.
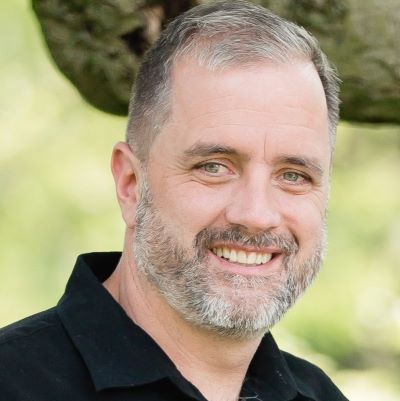
Along with additional space to produce wood components, the facility is adding new machining equipment and a flat line finishing operation that will complement its existing spray booths. The company also is looking to add another 50 workers on top of its current 250 between now and the first half of 2022.
But even with the expansion, it’s hard to predict when lead times might come back to a more normal six to eight weeks.
“That’s everybody’s question,” Stoltzfus said. “Once we open the factory that is going to help. That is going to have to happen or orders will have to slow down.”
“Even if orders would stop today, we would still have orders for a half a year,” he added. “I don’t expect it going back to 6-8 (weeks) anytime soon.”
Like some other wood furniture producers interviewed for this story, Palettes by Winesburg said it also has an ongoing moratorium on new accounts to keep the focus on existing customers. But it is not necessarily set in stone, Stoltzfus noted.
“We do allow for some expansion, but we are very selective and very careful,” he said, noting that the company will likely need to continue that selective stance for another year based on current demand. “It is about developing regions.”
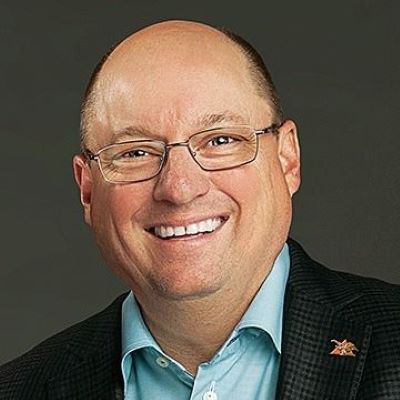
Not every company interviewed for this story is experiencing rising backlogs for their domestic wood business. For example, Ashley Furniture CEO Todd Wanek told Home News Now, “Our backlog is improving every day. In December, we’ll have a massive amount of inventory coming into the system and we will be able to serve our customers on a faster basis.”
Wanek added that the company’s employment growth also has improved, in part due to boosting worker wages.
“We have increased our wages substantially and have been seeing great results throughout our operations,” he said. “We’re optimistic about the future and our continued efforts in building our employment base across the board.”
Wanek also pointed to the company’s planned $1.5 billion investment focused on “manufacturing and distribution, automation, technology, and talent and future workforce. We’ve stayed vigilant in our mission throughout the course of this year. Specifically in the area of domestic case goods, we’ve invested heavily into automating our operations which has increased our production and kept our operations going strong.”
He added as the largest manufacturer of furniture in the U.S., Ashley has maintained a continued focus on “improving our operations and increasing capacity every day. In addition to our operations in the U.S., our Asian operations are doing an amazing job in supporting our operations and chipping away at our backlog on a global scale. Since operations have begun re-opening in Asia, we are seeing a strong increase in inventory, which will allow us to better serve our customers on a more timely basis and also take market share.”
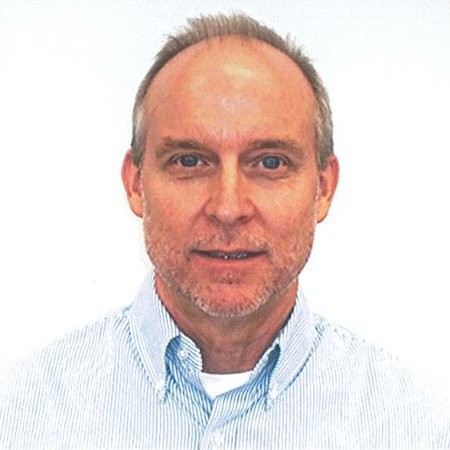
Legends Furniture said it, too, has lowered lead times for its domestic wood mix, which includes home entertainment and home office furniture.
Current lead times from its Tolleson, Ariz. factory are two to four weeks, probably among the lowest, if not the lowest, of any wood furniture producer in North America right now. That’s down from 16 weeks in May.
This drop has occurred despite a 35% increase in wood furniture sales year to date, compared to an 18% increase for imports, or 30% overall on the wood side.
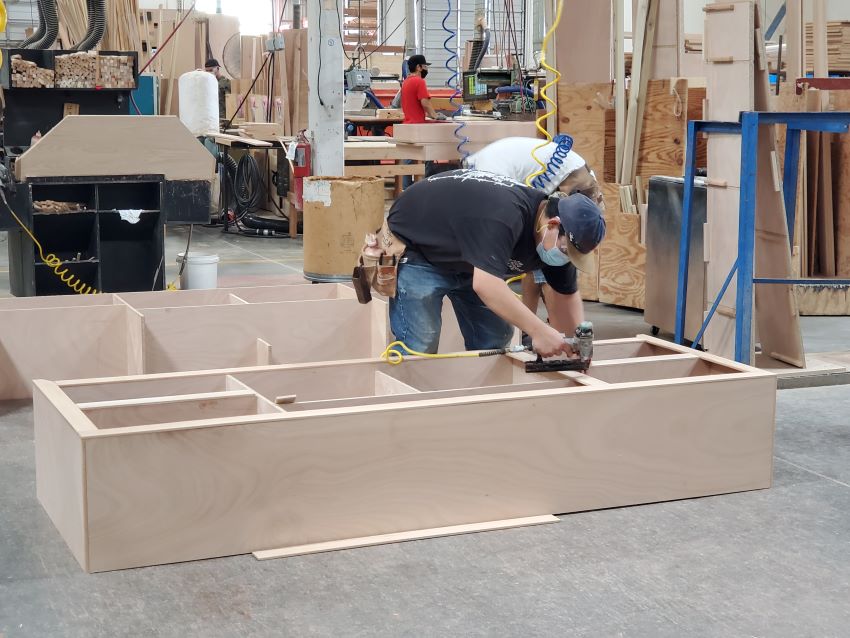
The company achieved this milestone recently by increasing its work force to about 150, up more than 10% pre-Covid. It also has reduced its SKU count by about 200 of its slower moving items, a 50% decrease, said Tim Donk, director of marketing and business development.
“That has made a big difference,” he said, adding that the company also worked a lot of overtime over the summer months. “We were working hard to bring everything down.”
These two examples, however, appear to be more the exceptions than the rule on the wood side of the business.
“In general I am convinced that these backlogs will take a long time to work out both domestically and internationally,” said Gat Caperton, CEO of Berkeley Springs, West Va.-based case goods manufacturer Gat Creek. “Who knows if the domestic producers will be able to add capacity faster than international, but both are going to be slower than anyone wants.”
“At the end of 2022 we may start seeing improvement,” he added. “But I would suggest it will be (sometime in) 2023 before both international and domestic producers start making real differences for the consumer. I think it’s going to be true not just in furniture but also in most durables.”
He said domestic wood producers in particular are just not used to the increases in demand that are requiring added capacity.
Gat Creek is expanding its 100,000-square-foot facility by about 40,000 square feet. But the project has run into some delays of late ranging from engineering issues with an expanded parking area to delays in getting steel for the building.
“We had our steel scheduled to arrive in April 2022 and now it is pushed to November,” Caperton told Home News Now, adding that it will take about 120 days from the time the steel arrives until the building is ready to occupy.
The bottom line? The company originally planned to have the expansion online by late October 2022. It will now be closer to April 2023, Caperton said.
But demand hasn’t slowed. Even with an additional 10 people on board since early August — which brings the plant up to 165 workers – the company’s lead times have risen to about 22 weeks, compared to 18-20 before the summer. Caperton noted that long lead times also result from Covid-related absenteeism to machines breaking down from longer than typical use.
“It is fortunate because of high orders and because production has been consistent,” Caperton said, noting that historically, lead times are from four to six weeks.
“That is where we would like to get in the future,” he said, noting it too is being careful about taking on new business right now. “We find that to be a pretty reasonable time frame, but it will take a long time to get there… It will take years for everybody — it’s just hard to catch up.”