350,000-square-foot operation in Salt Lake City will serve customers in Western states
SALT LAKE CITY, Utah — Upholstery manufacturer Albany Industries is adding a 354,000-square foot manufacturing and distribution center here that will service customers in the Western part of the U.S., a growing part of its business.
Expected to begin shipping in late June, the facility will be the company’s seventh manufacturing facility in the U.S. Its other facilities are in New Albany, Pontotoc and Calhoun City, all in Mississippi, as well as Galax, Virginia; Bay Minette, Alabama; and Tampa, Florida.
These other facilities largely serve customers east of the Mississippi although the company does service some customers on the West Coast. But those customers have been asking for distribution that is closer to their region, as it would significantly reduce delivery times and transportation costs.
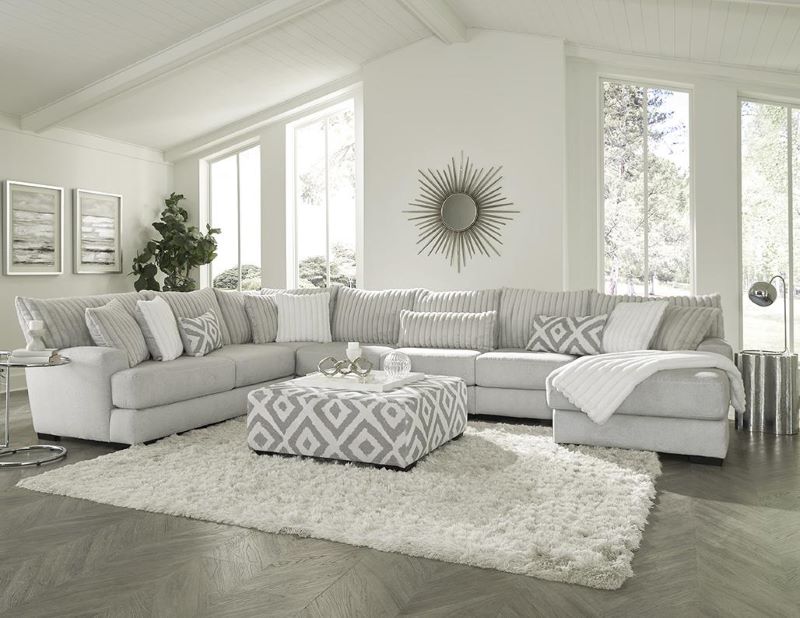
“This facility will give us the reach to service all of the Western U.S.,” said Craig Zielinski, chief operating officer. “Some of that we are servicing right now as we’re getting over into Texas a little bit. But the farther out you go it just get a little tricky on freight. … We’ve already got a lot of interest so that obviously reduces our business risk.”
Part of a multiphase project, the facility will handle light assembly of stationary and motion upholstery such as sofas, loveseats and sectionals as well as some occasional pieces such as accent chairs, chaises, swivel chairs and ottomans. Many parts and components initially will come from its global supply chain in Vietnam, China and Mexico, although over time, the facility will become more and more vertical, duplicating the footprint of its other domestic facilities.
“What this allows us to do is leverage some of our imports and get the best price and really deliver a broader offering to our customer base,” Zielinski said.
The plant and distribution center ultimately will mirror capabilities of its other facilities, providing what the company considers a unique product to its customers.
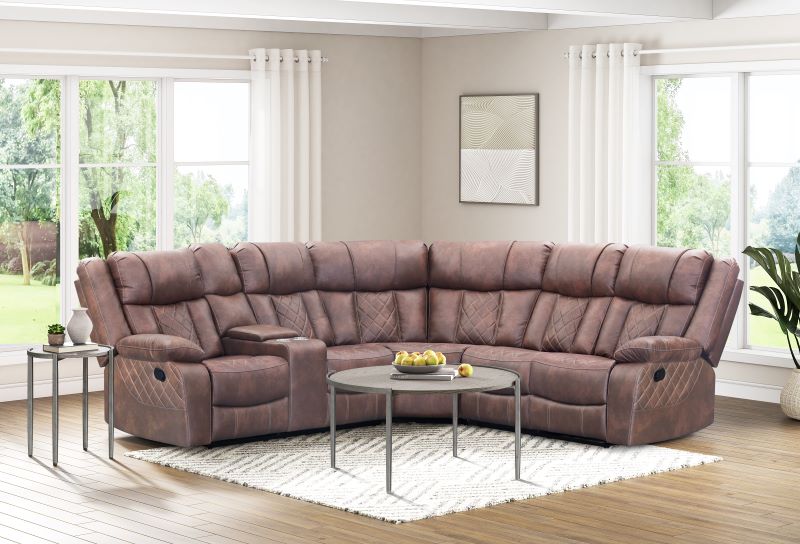
“Albany has enjoyed tremendous growth in recent years by offering unique home furnishings products with exceptional value to the U.S. marketplace through utilizing our extensive global supply chain and operating facilities,” said CEO Mark Gosnell. “Currently our operations in three countries and four states enable us to provide exceptional service and value to U.S. retailers. The addition of our Salt Lake City operation will facilitate our increased presence in the western U.S. and provide exceptional support for our retail partners in that region.”
The project will be developed in phases, ultimately building up to the type of operations it offers in its other domestic facilities.
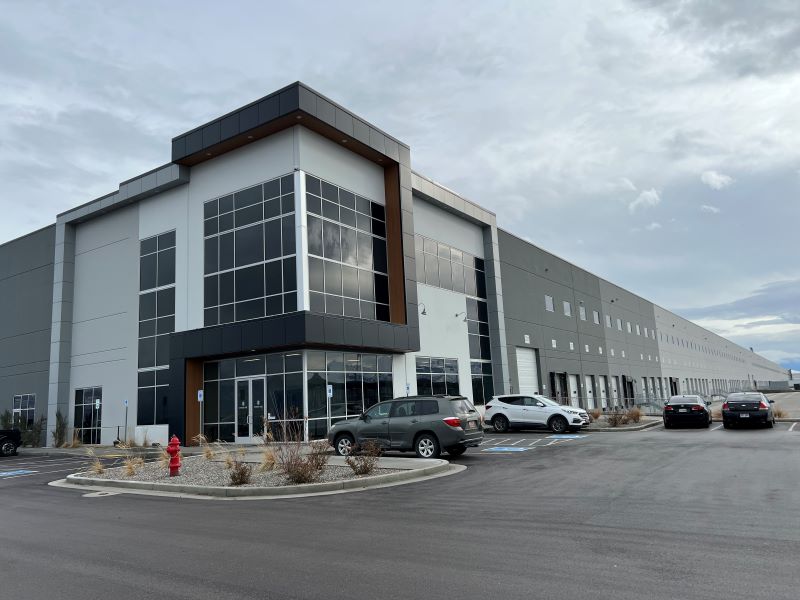
“The level of vertical integration at least initially will not be there, but that part will be growing, too,” Zielinski said. “It is what we know how to do and is core to our DNA. We are a manufacturer. Long-term, this is not going to be an all-import kind of business.”
While declining to offer specifics regarding a timeline or different phases of development, Zielinski said those details will emerge over time as the business dictates. This includes the amount of production that will be devoted to stationary and motion, which also will be based on customer demand.
As much merchandise will be built for inventory, it will offer quick-ship capabilities, particularly for bestsellers. That in turn is expected to minimize the risk for retailers not wanting to hold inventory of certain products.
Freight cost savings to customers, Zielinski noted, also will depend on their location in the western half of the U.S.
“If we are not better — and we are by the way — than what it costs to ship out of Northeast Mississippi, there is no value to the customer,” Zielinski said of the lower freight costs associated with the new facility. “We need to provide that savings for them.”