Company President Stephen Jensen recently shared thoughts with Home News Now about opportunities and challenges in Vietnam
HO CHI MINH CITY, Vietnam – Recently bedroom resource Maxwood Furniture announced that it has more than doubled the size of its factory here to about 1.3 million square feet.
The expansion is notable in that it gives the company increased production at a time when retailers are still seeking product for their floors and warehouses.
Completed in late 2021 and opened at the start of this year, the expansion added 300 workers to the mix initially, bringing the current workforce to around 1,400. When the facility nears full capacity, this number is expected to grow again to 1,800, the company has said.
In addition, it will boost production from 100 containers a month to 175, a number that eventually is expected to reach 225 per month at full capacity.
But like other manufacturers, the company is operating in a tight labor market that makes it a challenge to find and retain the right people for the job. Container pricing and availability also remain a key issue moving forward.
Company President Stephen Jensen recently addressed this and other issues facing Vietnam’s furniture industry. Here is what he had to say on the subject.
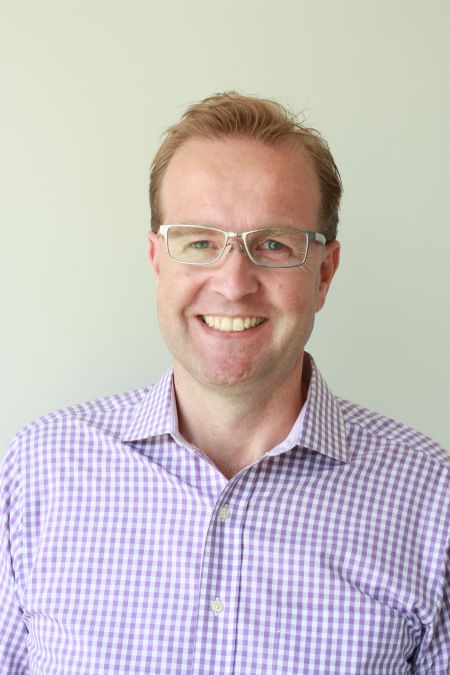
Home News Now: Can you say what the labor situation is like in the Ho Chi Minh City area currently? And how is it affecting Maxwood’s expansion?
Jensen: Our factory is located in Dong Nai province. Our facilities are brand new and state of the art, which helps us retain and hire the right people. And we have a strong management team who have created a strong culture/team spirit that has enabled us to work throughout the pandemic. Based on which we’ve been able to not only successfully retain workers, but also hire an additional 300 workers to support our recent expansion.
It sounds like you will be adding even more workers in the near future. How did Mawood manage the disruptions during the pandemic up to this point?
Jensen: Our factory currently employs 1,400 workers, growing from 1,100 prior to our Q1 2022 factory expansion. We plan to grow to 1,800 workers by 2023. It is a testament to our amazing Vietnamese team, who decided to quarantine on-site in the factory for 10 weeks (this past summer) so we could keep operating. Our factory was one of 400 factories that remained open…so we have not had any production disruption and have been able to retain workers.
Do you expect labor shortages to affect Maxwood’s ability to find workers beyond what you have in place today?
Jensen: Due to measures taken (such as offering vaccination to all workers and quarantining) we have had the advantage of operating through the “Covid-19 shutdown” in July, August and September. We therefore did not experience the issue of workers not returning to work, meaning that recruiting efforts continue to focus on expanding versus maintaining work force numbers. We’ll be looking to recruit an additional 400 workers throughout 2022 and don’t anticipate issues in doing so given our solid reputation, state of the art facilities and strong culture.
Are you having to train or retrain any workers to get them up to speed on your manufacturing process? If so, how is this going?
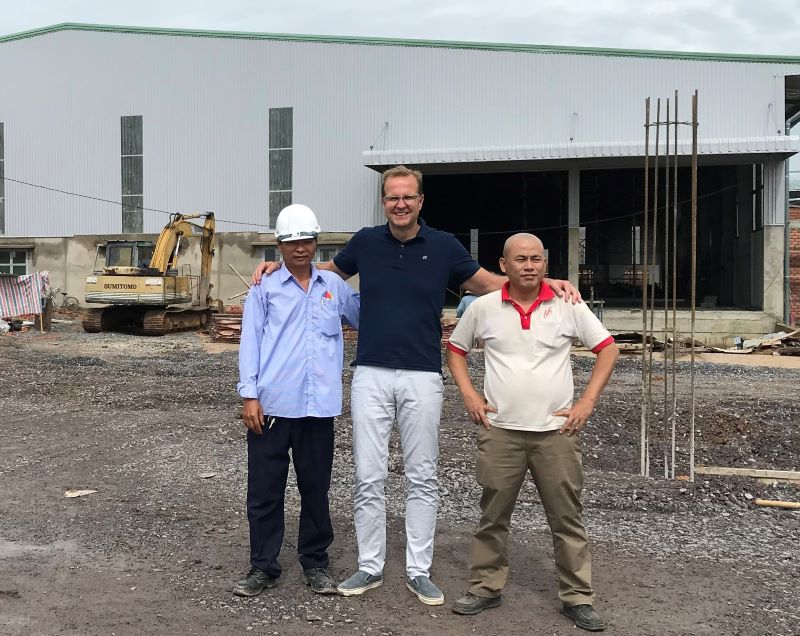
Jensen: We train our new workers in seven days then “buddy them up” with experienced workers for 30 days. We have gained efficiencies in our manufacturing facilities by investing in state-of-the-art equipment that automate many steps of our process and reduce dependency on skilled workers.
Are you having to offer any incentives to bring new workers on board?
Jensen: Yes. All of our workers sign a full-time contract after which they receive benefits such as medical insurance.
What are lead times like presently compared to what they may have been in recent months? Are you able to reduce lead times any with the additional workers in place?
Jensen: Our lead times have remained reasonably consistent – 45 days production plus 45-60 days shipping. While we have experienced limited disruption in our factory operations, we have experienced shipping delays. However, contracted rates and strong relationships within the shipping industry have enabled us to limit this impact.
What about your ability to procure materials in and outside of Vietnam? Can you say how this has affected your production or lead times?
Jensen: Our advantage is that we make material orders well in advance and hold a supply in our warehouse. So if we have problems with materials shortages, we can use our inventory or have time to find a local supplier.
What do you see as the biggest challenge moving forward as it relates to your manufacturing in Vietnam? Is it labor, or securing containers or bookings on a vessel?
Jensen: Shipping remains our biggest challenge as there is only so much within our control. Like everyone else we see significant delays shipping containers…as the ships can’t offload.