Earlier this past spring, Home News Now visited the Jasper and Ferdinand, Indiana, manufacturing operations of Best Home Furnishings, an upholstery manufacturer whose line includes motion and stationary upholstery.
Here we got to see the processes involved in the production of products ranging from recliners and swivel chairs to stationary sofas, loveseats and accent chairs, to name several core items in the line. With an estimated 1.1 million square feet spread over several facilities, including a dimension plant that produces wood components for upholstery frames, production starts with the cutting of raw lumber to the cutting of fabrics and upholstering of the entire seating line.
Of course, the company’s team of manufacturing talent, estimated at about 725 men and women, is its most important asset. Here we captured them at work bringing the line to life for retailer customers around the country. Scroll down below for a glimpse at the operations and people inside this storied upholstery manufacturer.
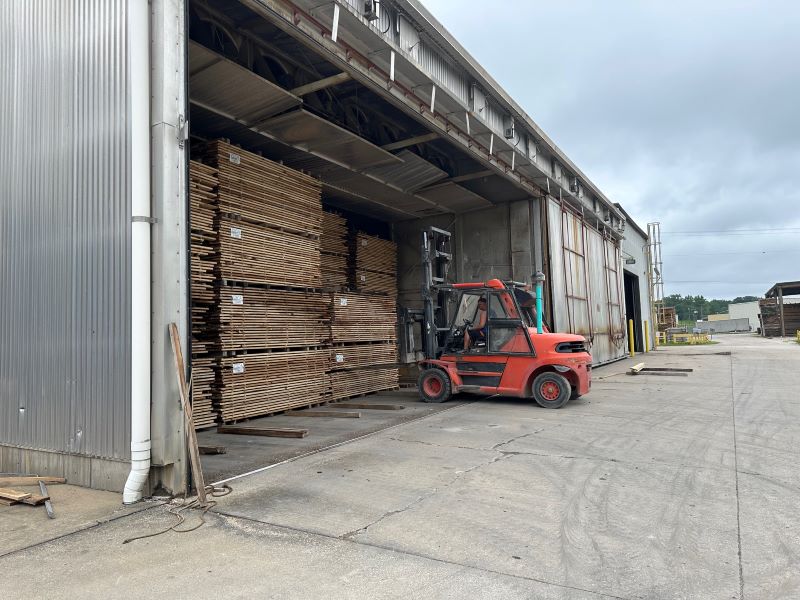
Lumber is stacked inside dry kiln facilities at the company’s dimension plant in Jasper. Two facilities on-site handle some 70,000 board feet of poplar and soft maple, woods that are known for their ability to bend for use in curved upholstery frames.
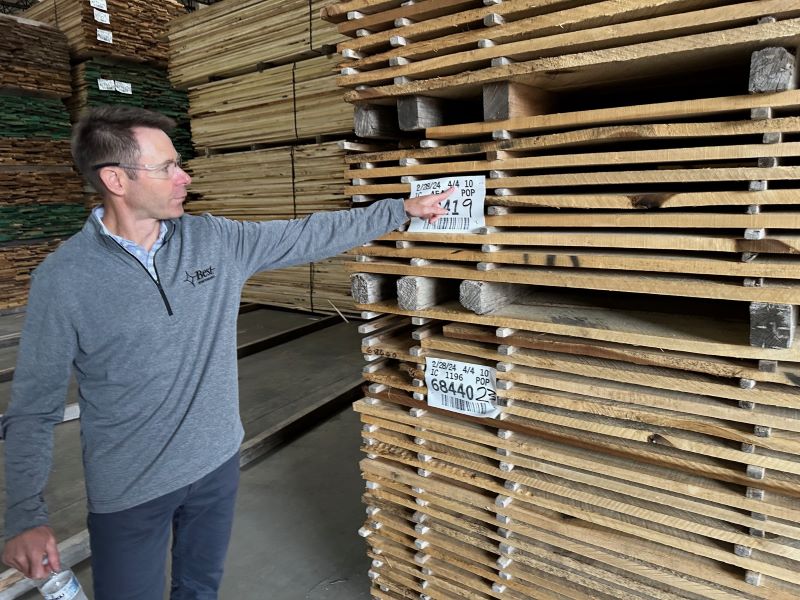
Eric Vollmer, senior marketing strategist, points to a stack of wood that has been treated for several days in the dry kiln ovens. The tag he is pointing to shows the date it was kiln-dried.
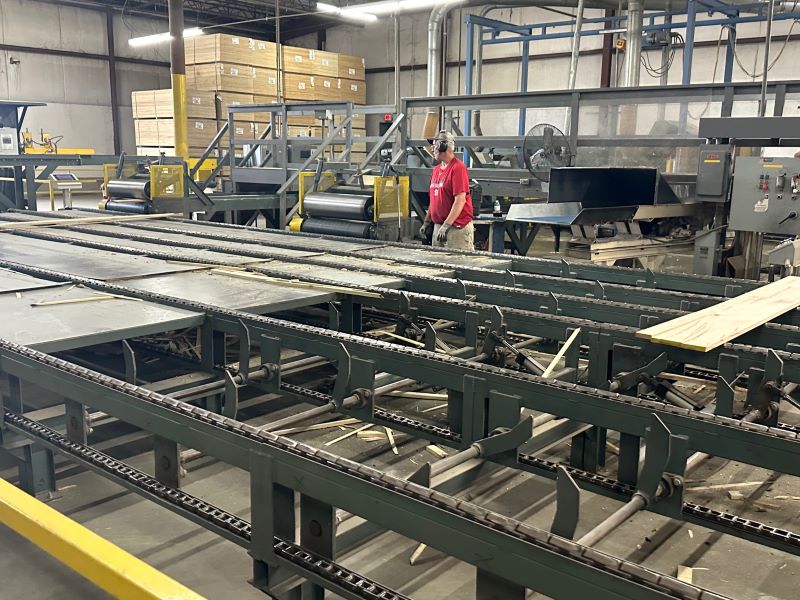
Boards are seen being cut to specific lengths at the dimension facility in Jasper.
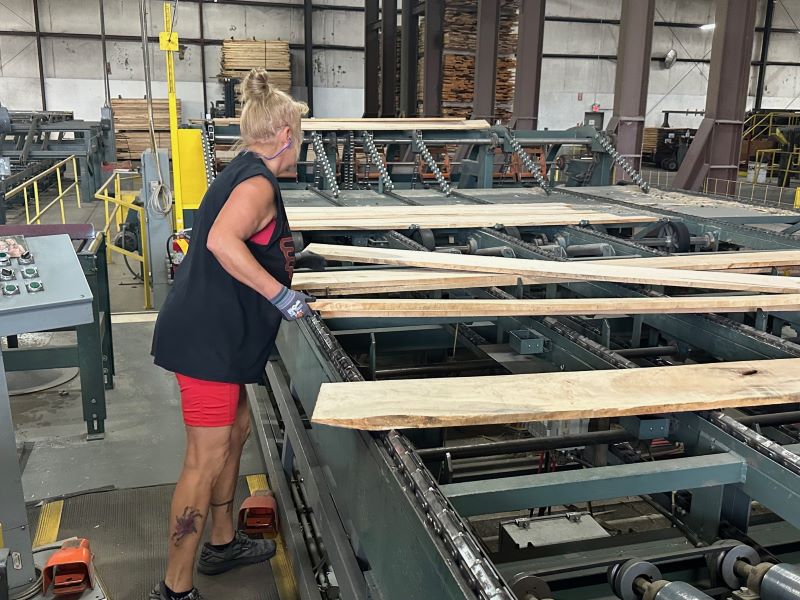
More boards are seen on their way for further processing that will smooth the edges and take out various defects.
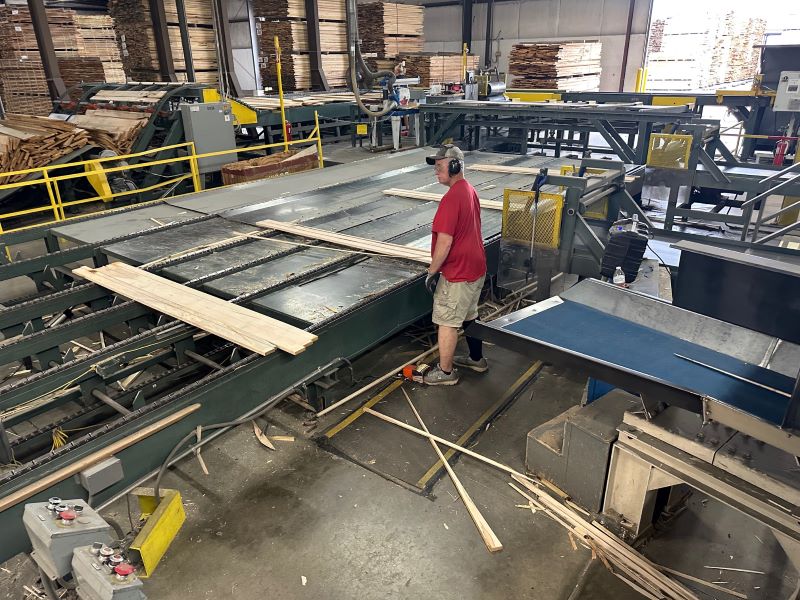
More planks of lumber are seen making their way through the dimension plant.
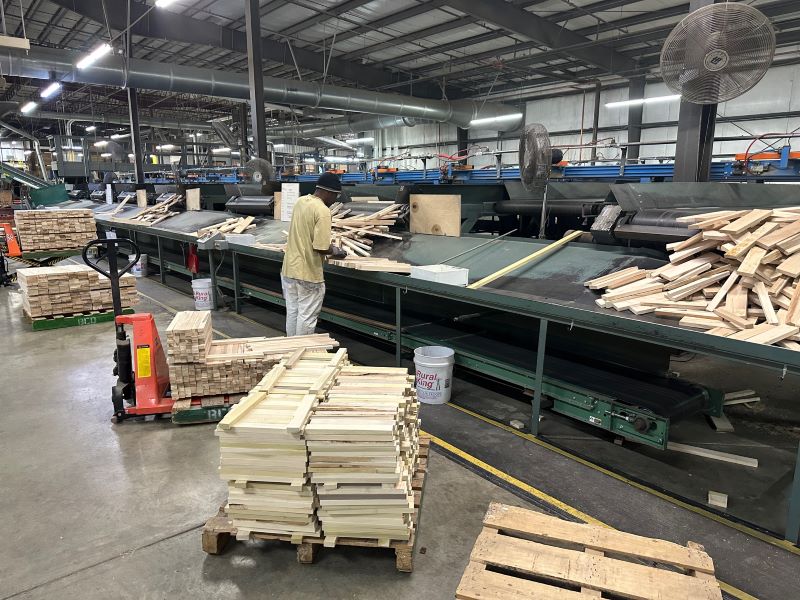
Wood that has been cut to various sizes is seen being sorted for use in upholstery frames.
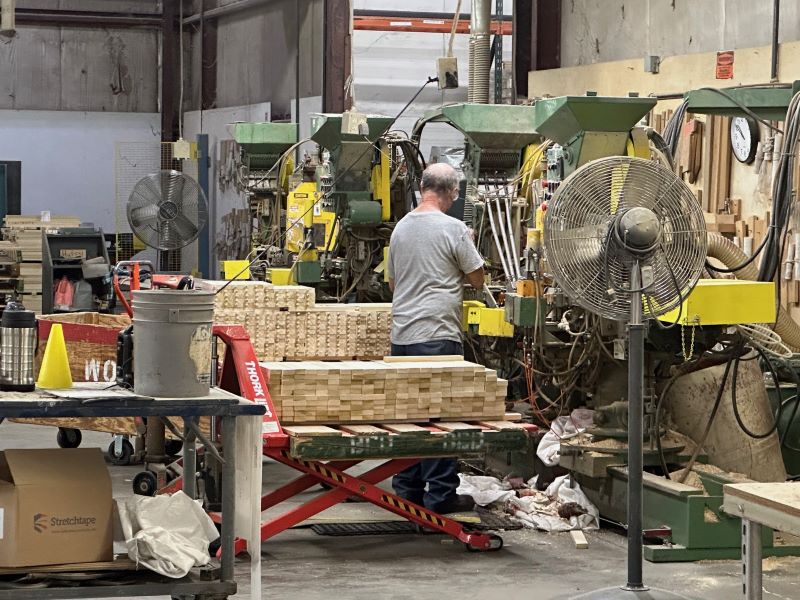
Wood that’s been cut to specific sizes for just-in-time inventory is stacked and prepped for use in the upholstery line.
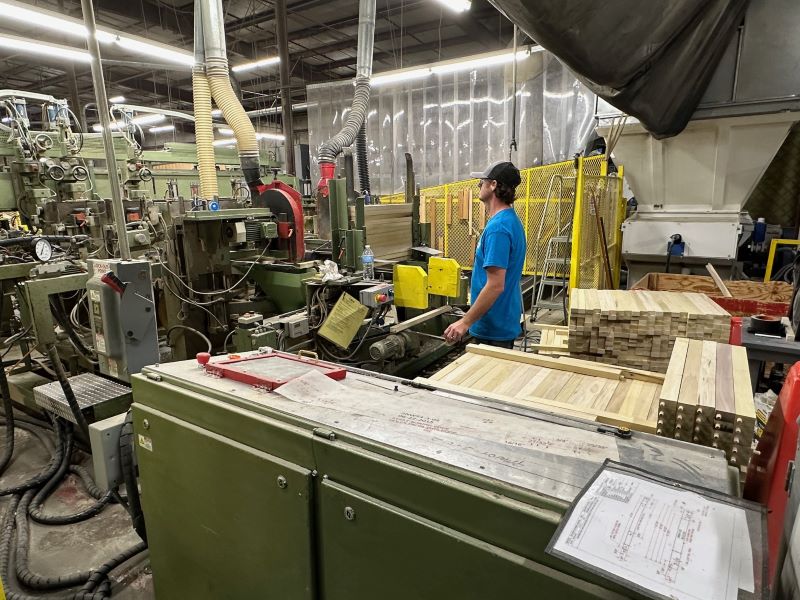
More stacks of wood cut to specific lengths are seen going through more smoothing and sanding to meet the company’s high standards for wood components.
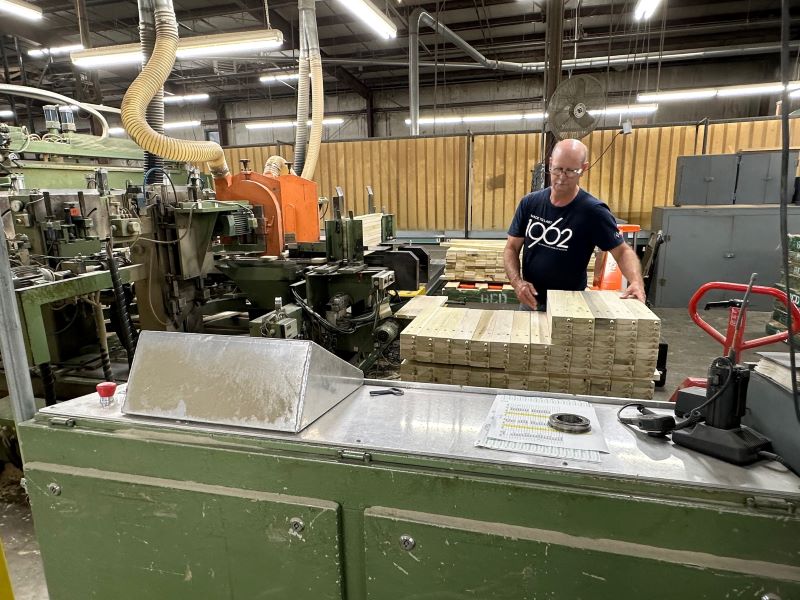
These boards are shown with wood dowels, another step in the wood processing that will create more stability when pieced together with other wood parts used in various frames.
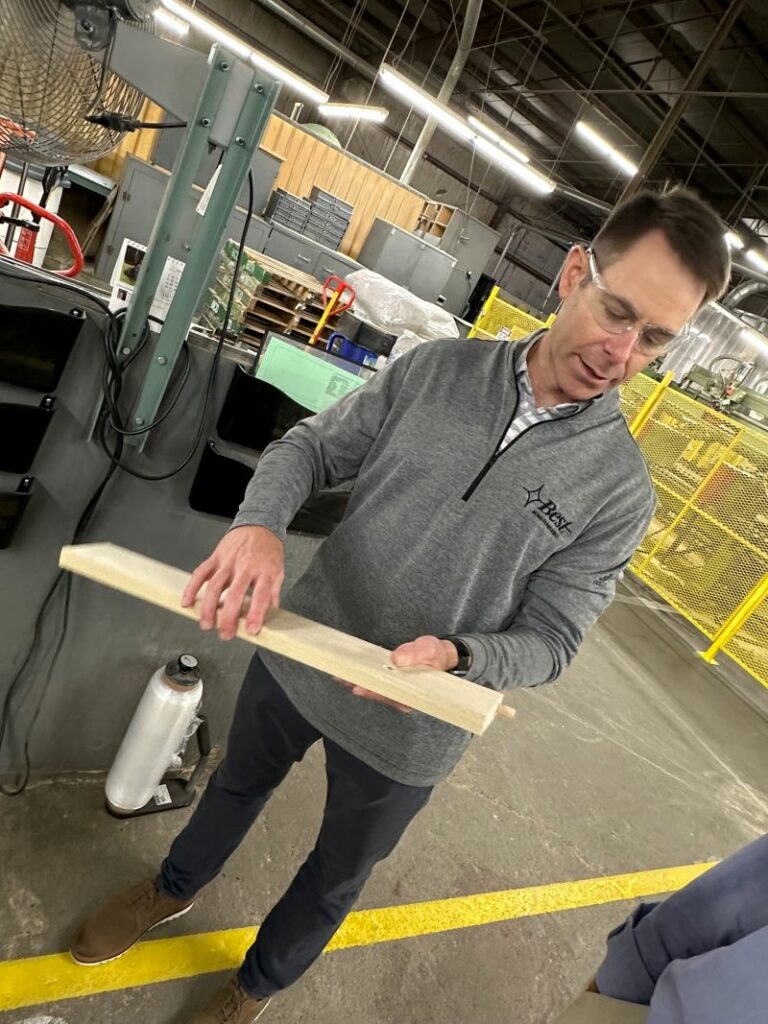
Vollmer holds up a solid wood plank to give a closer look at the wood dowel construction mentioned above.
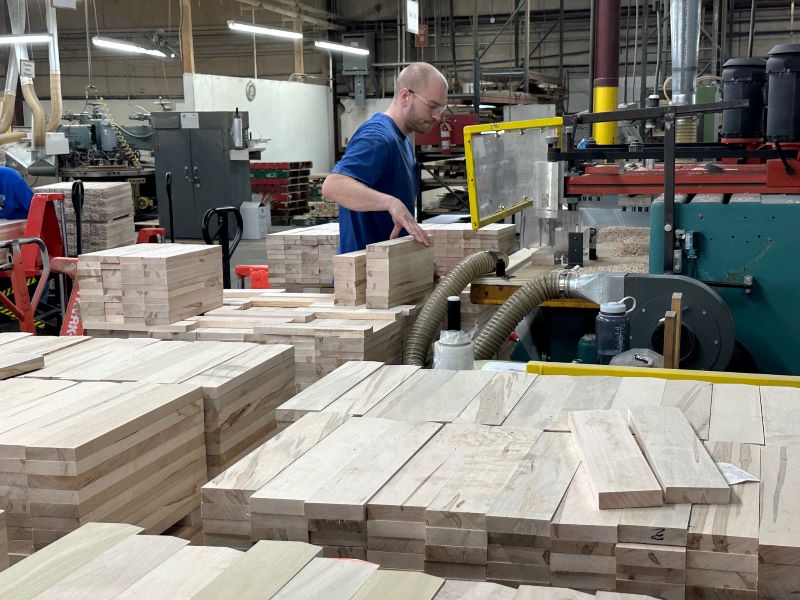
These smooth planks of wood are just a glimpse of the thousands of board feet that move through the dimension plant each day.
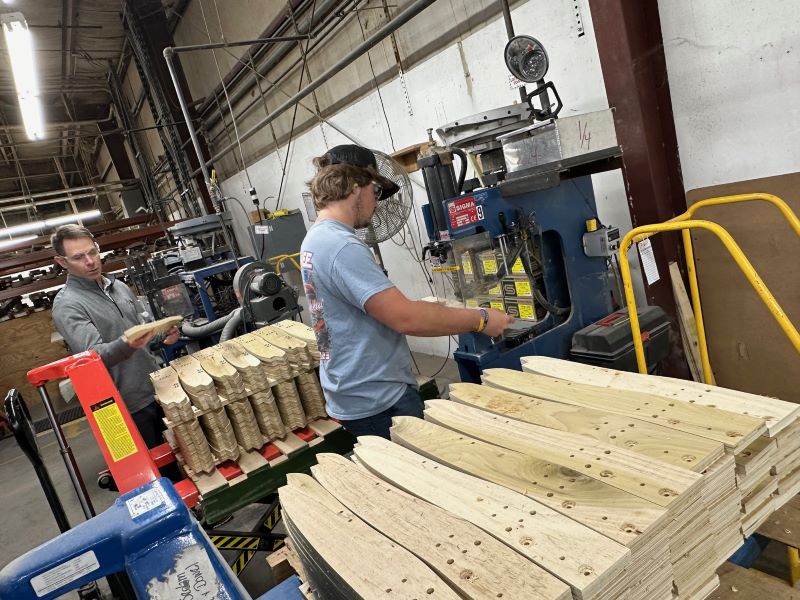
Vollmer holds up a section of wood to show the further shaping that’s done for the wood frame on this saw.
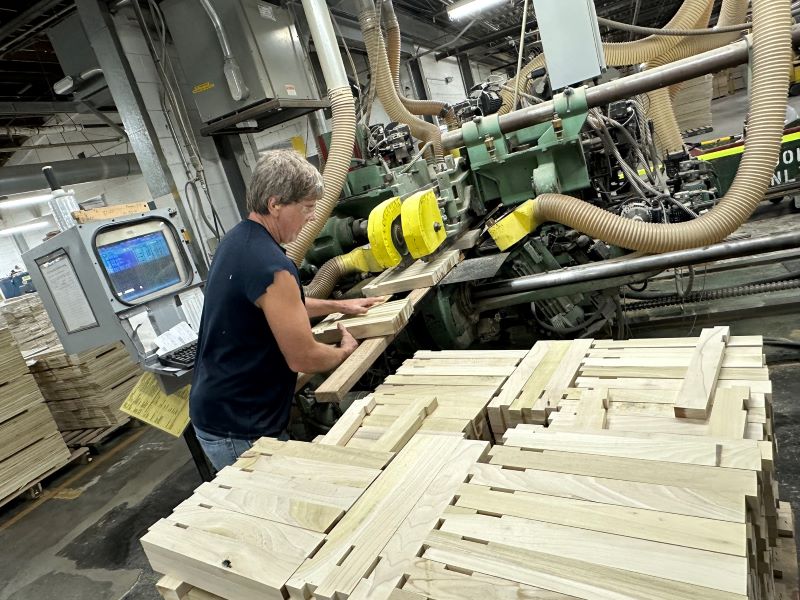
These boards show further shaping that will provide structural integrity for various frames when they go through further assembly.
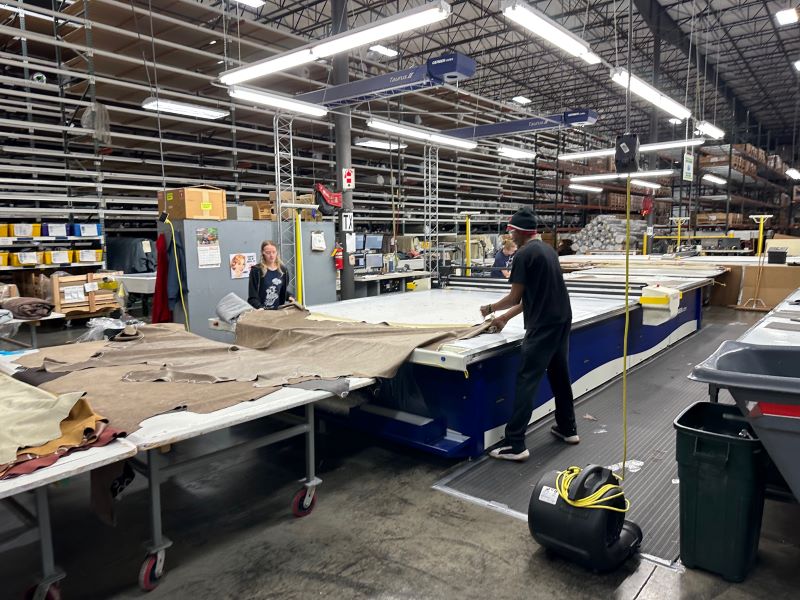
At the Ferdinand plant, workers are seen spreading leather hides over tables that will cut them to various shapes and sizes.
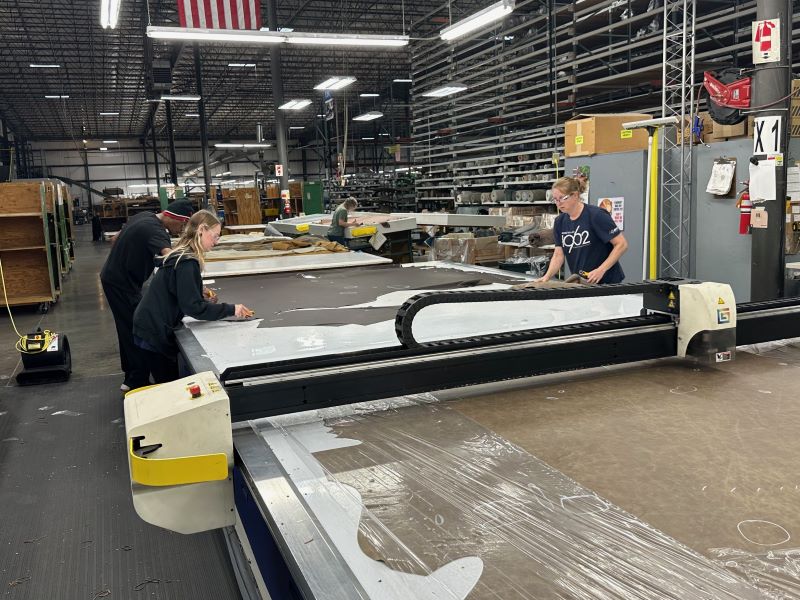
More hides are laid out with markings showing places to remove defects and cut various patterns.
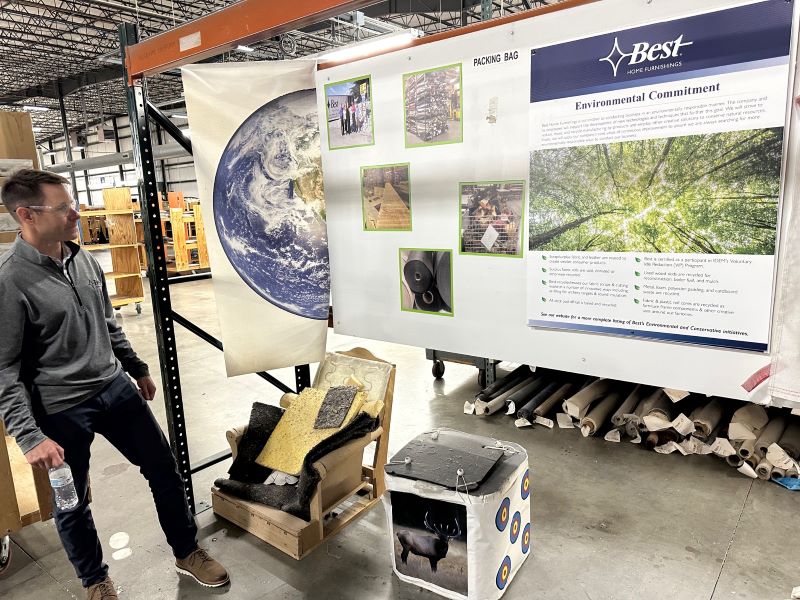
Vollmer shows a display at the Ferdinand plant that illustrates different ways the company is committed to a sustainable manufacturing approach.
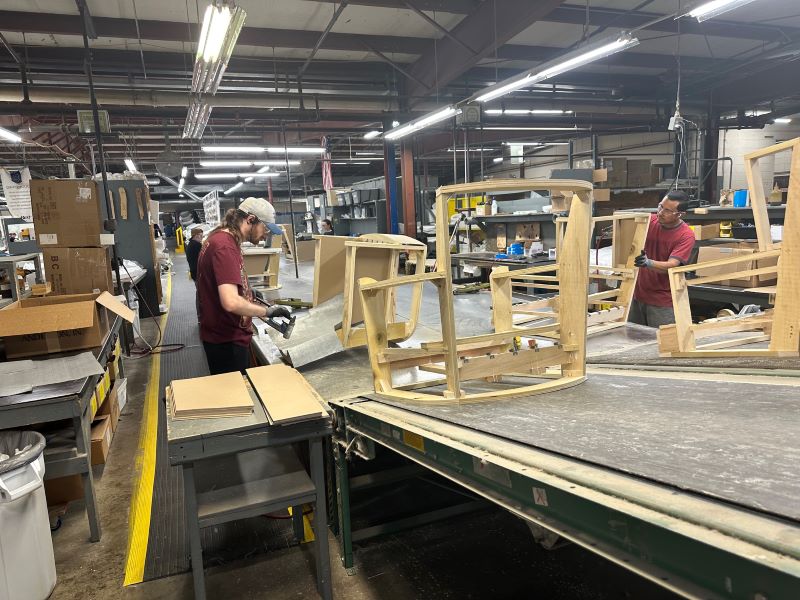
Chair frames are seen being built at the Ferdinand plant.
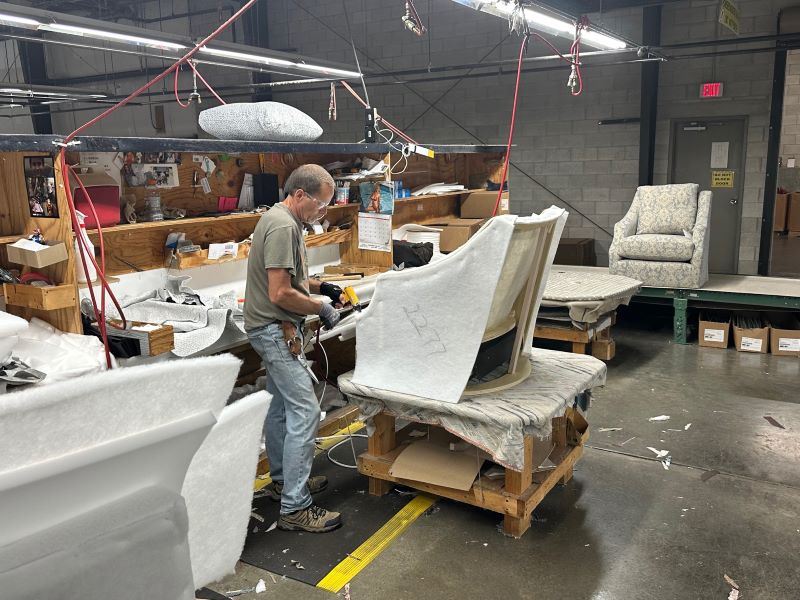
Layers of foam and fabric are seen being applied to chair frames in the photos above and below.
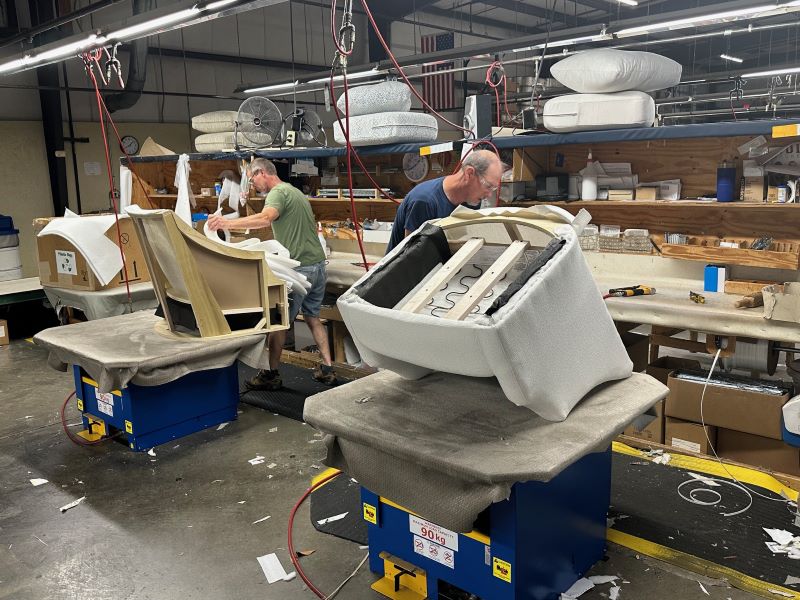
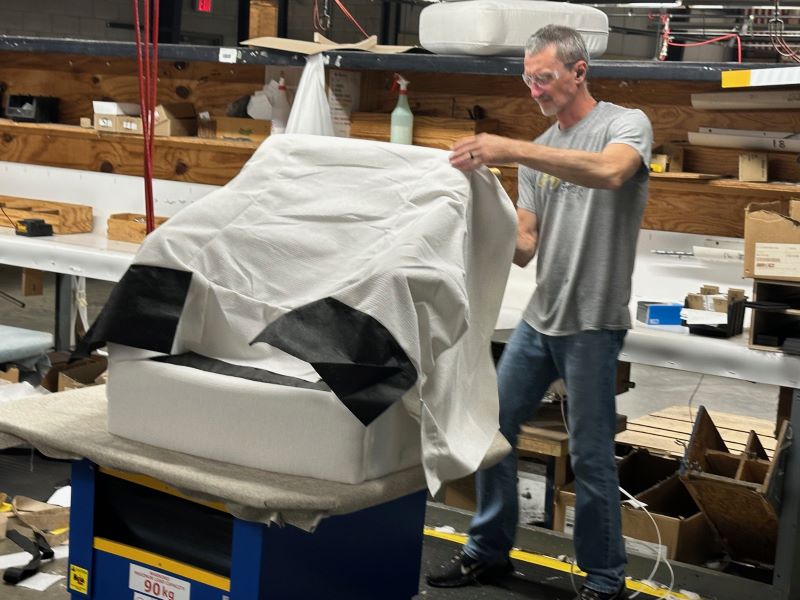
A worker seen further up the production line is applying layers of foam and fabric to a chair frame in the photos above and below.
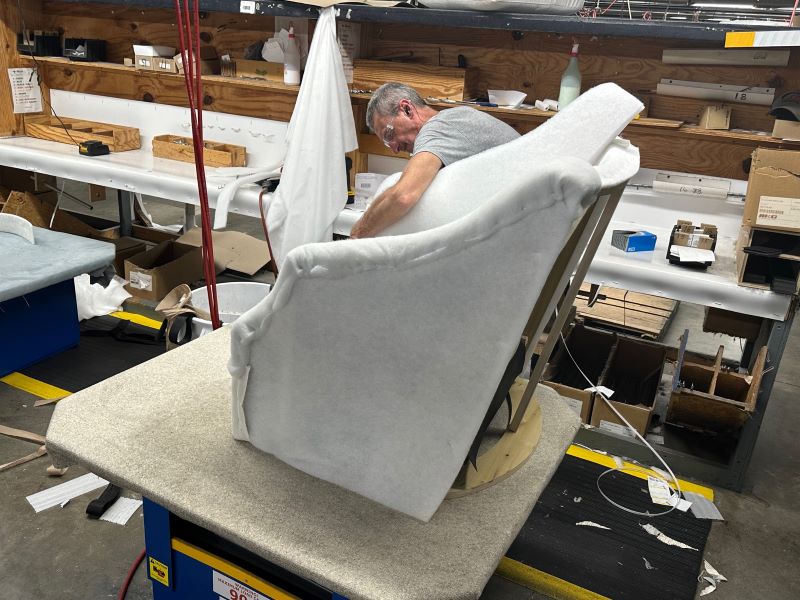
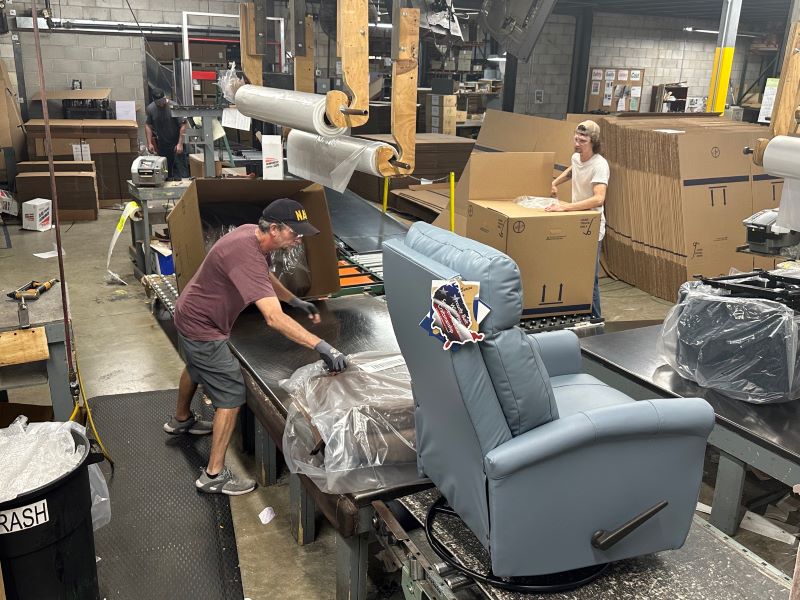
Workers in the packaging area are seen preparing finished product to be secured in a box for shipping.