Devastation from storm caused a significant loss of inventory that is requiring the company to rebuild orders for its custom line
MORGANTON, N.C. — Just over three weeks from being bombarded by Hurricane Helene, luxury furniture manufacturer EJ Victor remains in recovery mode and does not anticipate resuming manufacturing of its upholstery and case goods lines until the beginning of January 2025.
But the company is making progress and will be at the High Point Market starting later this week and running through Oct. 30. With inline product already in the showroom, it also will be taking orders for its Shamsian and Antonia case goods collections as they are being shipped from facilities that were not impacted by the hurricane.
The storm that struck Western North Carolina Sept. 26 ravaged the company’s Morganton production facilities, leaving more than 2 feet of water in both the plant and neighboring administrative offices. This was caused by flooding from a nearby river whose banks overflowed and damaged the plant and surrounding properties including a nearby nursery.
The dollar value of the damage was not available as the company is still working with insurance adjusters to determine the full extent of what was lost. But company CEO Richard Oliver told Home News Now that the main damage was to inventory, ranging from raw materials including frames in its warehouse to products including goods waiting to be shipped and various works in progress. Other materials that were stored on racks higher up largely escaped damage as did most machinery, which Oliver said the company has tested to ensure it is in working order.
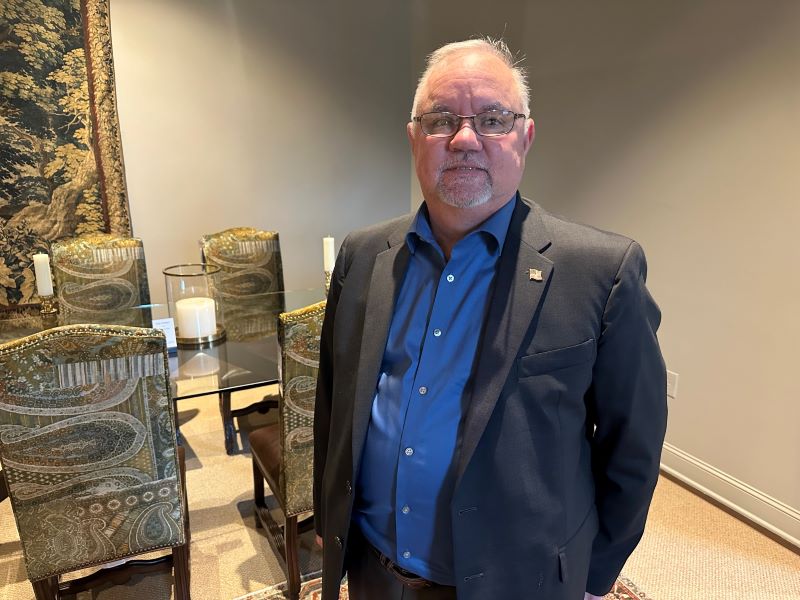
Its offices were also damaged as the water flooded that part of the building, damaging some office furniture, supplies and records. But since it is on a cloud-based ERP system with data management equipment positioned at a higher level, the company said its financial data and other information necessary to run the administrative part of the business is intact. Some employees are also starting to return to the office as the facilities have been thoroughly dried with wet vacs.
Oliver explained that the loss of inventory is what has caused the delay in production until the start of next year, with product expected to ship sometime in early to mid-February.
“That is what causes your disruption,” Oliver said. “Because in an industry where you have anywhere from five- to eight-week lead times being the norm, if you get wiped out of your inventory base, you are eight weeks behind now on things that need to get out the door. So, by far, that was the most impactful loss that we had, not just from a dollar standpoint, but just in terms of the disruption for us and our customers.”
The company has discussed having some products produced by other area suppliers. But because of the highly custom nature of its business, most are not willing to do that on a short-term basis. It also would be highly selective in who it chooses to manufacture its products whether it be upholstery or case goods, the vast majority of which EJ Victor produces in its domestic operations.
“With a brand like ours, we are at the top end of the industry,” Oliver said, noting that the goal is not to just put the company’s highly customizable line in the hands of any manufacturer as that could compromise quality for it and its customers. “It’s got to be someone who is as crazy about quality as we are.”
Right now, he said, customers have been extremely supportive, having come to realize what it’s been through in recent weeks. And for that he is extremely grateful.
“In this situation, which was totally an act of God, all of our folks are very understanding,” he said. “I have literally talked to folks that represent the vast majority of our business and they all seem to support us getting back up and running.”
“We are just looking at where the opportunities are and are trying to forge forward and do everything we can to treat our partners and our customers right,” he added. “I think when you do that and you have the right values in a relationship, then most of your customers have those same values and they support you in a situation like this. And that’s exactly what we have found.”
Oliver also thanks the workers who have stepped up to the plate to help the company clean up the damaged areas and restore the operations as well as the community at large which has provided much-needed supplies such as water and other items to those company team members in need.
With market almost here, Oliver said that customers will be able to come to the showroom at 116 S. Lindsay St. to see some new and inline product and even buy certain items off the floor at the end of market.
“We don’t always sell off our floor samples,” he said. “A lot of times, we’ll keep them for two or three shows. But in this case because we know that product availability is going to be a bit of an issue in the short term … if folks would like to buy samples this time, particularly from the EJ Victor brand and the Antonia brand, we are going to have floor samples available for purchase just because there are certain folks that need it and need it now.”
He said that despite the challenges, he hopes that customers come to see EJ Victor at market starting later this week.
“There are certain things that we had in process that would not make it to market, but the market itself is going to be a very positive event, and a very powerful event. And we would love to have everybody come visit us,” he added, noting that the showroom will have a cocktail event from about 5:30 to 8 p.m. Sunday at which it will also honor company co-founder John Jokinen, the longtime executive who transitioned into a new role as board chair this past spring.
Moving forward, he believes the company is in a good position overall thanks to operational improvements and measures it has put in place to make the business more efficient and customer-focused. Thus, it aims to resume production and shipping as quickly as possible.
“We hate to have something like this happen, but we were in a place of strength when it happened which made the recovery process a lot easier than it would have been say a year or two ago,” he said.