Latest Reshoring Initiative report identifies global factors that are driving manufacturing back to the US
HIGH POINT — Reshoring continues to be an attractive alternative for companies looking to avoid geopolitical risks overseas, shorten lead times and take advantage of government subsidies supporting economic growth.
These are among some of the key reasons that onshoring remains a driving force supporting the growth of businesses across a wide range of products and services, according to the Reshoring Initiative’s latest annual report published this month.
It identified factors such as Russia’s attack on Ukraine as driving reshoring and foreign direct investments from Europe to the U.S. because of factors such as natural gas and electricity availability and pricing. It also noted that reshoring and FDI from China are near historical highs as companies wish to avoid geopolitical risk, including U.S. and China tensions over Taiwan.
And although the Oct. 7 Hamas attack on Israel was too late in the year to impact 2023 data, it likely will have a ripple effect across various industries because of supply chain disruptions that will influence costs, materials availability and production schedules, not to mention high shipping costs, which the furniture and other industries are already experiencing.
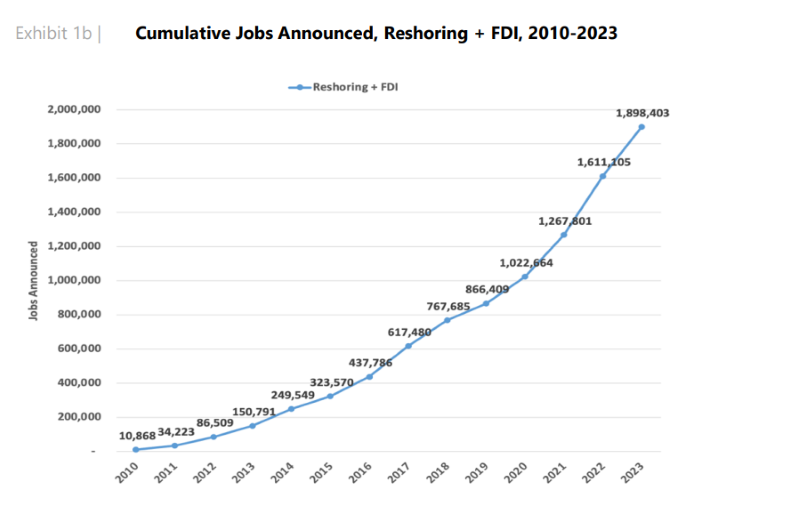
Despite these factors, there was a slowdown in the number of job creations relating to reshoring and FDI, the report noted. For example, in 2023, there were 287,299 jobs announced, the second highest on record since 2010. Some 52% of the jobs created in 2023 were because of reshoring and 48% were associated with FDI.
However, the number of jobs created was down 16% from the 343,304 announced in 2022. The report attributed some of the decline to a drop in government subsidies in industries such as EV batteries, solar energy and semiconductor chips.
Still, the numbers were up considerably from prior years, notably during the pandemic. For example, compared to 2021, the number of jobs was up 17.2% and nearly 85% up from the 156,256 jobs created in 2020.
For the furniture industry, the numbers are somewhat sobering as they highlight the industry’s continued reliance on offshore manufacturing and cheap labor, which drives prices down for consumers. It ranked among the lowest number of jobs created with 2,813, or 1% of the total, with 25 examples of expansions with an average of 115 jobs created per case.
While those numbers might seem impressive by themselves, the industry ranks in line with other lower job creating segments including primary and fabricated metal products, medical equipment and supplies, food and beverage, apparel and textiles and nonmetallic mineral products and wood and paper products, all of which were also at 1% of the total jobs created.
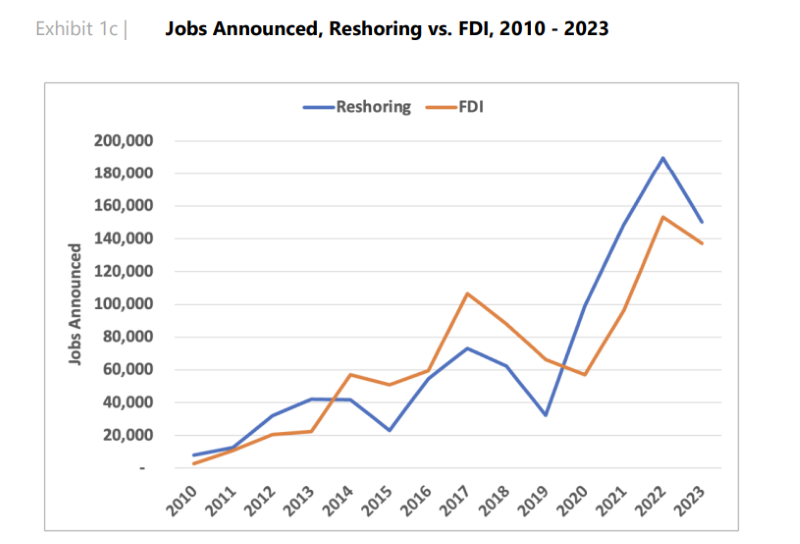
The industries with the highest number of jobs created related to reshoring included electrical equipment, appliances and components (105,557 jobs created, or 37% of the total); computer and electronic products (77,150 jobs created, or 27% of the total); transportation equipment (31,367 jobs created, or 11% of the total); chemicals (31,103 jobs created, also 11% of the total); machinery (12,646 jobs created, or 4% of the total); and plastic and rubber products (5,909 jobs created, or 2% of the total).
The report also provides a deeper dive into the factors that have driven or not driven reshoring or FDI initiatives. Here are several key takeaways:
+ Tariffs were not cited by companies as a major factor in reshoring. This is despite data that shows that U.S. manufacturing costs are estimated to be about 40% higher than China’s, which means that China is still cheaper by about 15% factoring in a 25% tariff. In particular, it noted that the Biden administration has not only maintained many tariffs, but also has expanded them on products such as electrical vehicles, solar cells, semiconductors and medical supplies.
+ The availability of a skilled workforce was the No. 1 criteria in site selection and reshoring site selection, the report said. “Clearly the U.S. skilled workforce lacks the quantity and quality needed for faster reshoring and is at a disadvantage relative to many other countries,” it noted, adding, “Nevertheless, about 49% of cases mention skilled workforce availability as a reason they reshored, essentially tied at No. 2 with proximity to customers. … We expect to see this factor become even more important as companies work to fulfill their massive commitments to domestic production.”
+ Disruptive events such as Covid-19 are present in the minds of manufacturers, cited as among the disruptive factors that are “now referenced as a reminder of the powerful impact future pandemics, wars, technology or climate events could have.” The report also cited a 2023 survey by Chief Executive magazine that said geopolitical risk exposure was the top driver for reshoring operations. For example, rising tensions between the U.S. and China over Taiwan were cited as a key factor involving companies that are considering reshoring as a critical part of their long-term planning.
+ The Israel Hamas conflict also was cited as having implications for U.S. manufacturing, particularly related to the pharmaceutical and aerospace and defense industries, including pharmaceutical manufacturers in Israel that have had to close or cut back their operations. The report noted that General Dynamics, for example, has had disruptions in its aircraft production related to issues with Israel suppliers resulting in delays and reduced deliveries. It also noted how the conflict has led to disruptions in shipping routes, namely through the Red Sea. As the furniture industry has experienced firsthand, this has affected costs and container availability.
+ The top five countries involved in reshoring/FDI efforts in 2023 included Korea with 20,360 jobs spread over 73 cases, China with 18,440 jobs and 71 cases, Japan with 18,192 jobs and 69 cases, Germany with 16,174 jobs and 71 cases and the United Kingdom with 14,739 jobs and 20 cases. In the Top 10, these were followed by Canada, India, Singapore, France and the Netherlands.
+ States with the highest number of job announcements related to reshoring/FDI included 1) North Carolina with 24,404 jobs over 87 individual cases, Kentucky with 22,752 jobs over 27 cases, South Carolina with 21,422 jobs over 92 cases, Georgia with 21,267 jobs over 72 cases and Texas with 19,057 jobs over 109 cases. These were followed by Arizona, Illinois, Indiana, Ohio and Tennessee in the Top 10. The South had the highest number of jobs created at 85,181 over 376 cases, followed by the Midwest with 30,074 jobs over 172 cases, the West with 22,106 jobs over 149 cases and the Northeast with 8,971 jobs over 87 cases.
+ Factors in the strength of the South included right-to-work laws that make it more cost competitive, low corporate and individual state taxes, higher incentives, and generally lower wages and property values that also support highly localized supply chains. “Much of the infrastructure is newer than in the North and it is easier to attract employees to relocate,” the report said, adding that in addition to well-supported vocational education institutions, the South has a manufacturing base that “extends across a broad range of industries, from high-tech chips and batteries, to low-tech industries such as food, furniture and apparel.”
The report also said that nearshoring — the movement of jobs to neighboring countries such as Mexico — has gained momentum because of their proximity to the U.S. market, which in turn shortens lead times. Citing the U.S. Census Bureau, the report noted that Mexico has overtaken China as the largest trading partner for the U.S. However, it added that its analysis of pricing differences and the flow of Chinese products through Mexico “suggests that the U.S. remains more dependent on China than on Mexico, particularly for products that are not readily obtainable elsewhere.”
Nearshoring and reshoring were major drivers of business for the furniture industry during the pandemic, particularly because of disruptions in the supply chain and increased costs of flowing goods from overseas. As those issues waned, the industry once again fled to Asia.
Now as container costs continue to rise, the industry perhaps is rethinking this strategy. As many have learned, there are plenty of benefits to having your product mix closer to home. The report simply highlights these benefits, if anything, communicating the importance of having a domestic resource as part of an overall diversified supply chain.