Attorney Michael Sullivan urges AHFA members to have a strong compliance program in place to deal with current, looming issues
COLFAX, N.C. — Compliance is one of those terms most people in or outside the industry try to avoid — at least until a compliance deadline is fast approaching like a train in a tunnel. The subject just bears too much technical and regulatory complexities for most to embrace it with any type of enthusiasm or passion.
Here’s another sign of how popular the issue of compliance is among our readers. For example, many of the hits on LinkedIn for many of our personnel stories about new hires and promotions are in the thousands: two, three, five, seven thousand more.
Stories about tip-over or formaldehyde regulations? It’s more like in the low hundreds — and understandably so because of the highly technical and engineering-centric nature of the subject matter.
All this came to mind during the American Home Furnishings Alliance’s Feb. 15 workshop on the looming March 22, 2024, deadline on the final stage of compliance with a federal formaldehyde standard being overseen by the U.S. Environmental Protection Agency.
The workshop was full of useful, yet extremely technical information that this journalist is still trying to wrap his mind around.
It included in-depth presentations from leading adhesive producers who discussed new and emerging resin technologies as well as a presentation from Robert Courtnage, lead physical scientist in the EPA’s Office of Chemical Safety and Pollution Prevention. He gave an overview of provisions in the standard relating to laminated product manufacturers and importers, which the rule refers to as fabricators.
In addition, Travis Snapp, Joel Oser and Chris Battin, all of Benchmark International, outlined some specific information that companies need to know relating to the March 2024 deadline, including labeling requirements for exempt laminated products and what companies should know and be prepared for if they don’t qualify for an exemption.
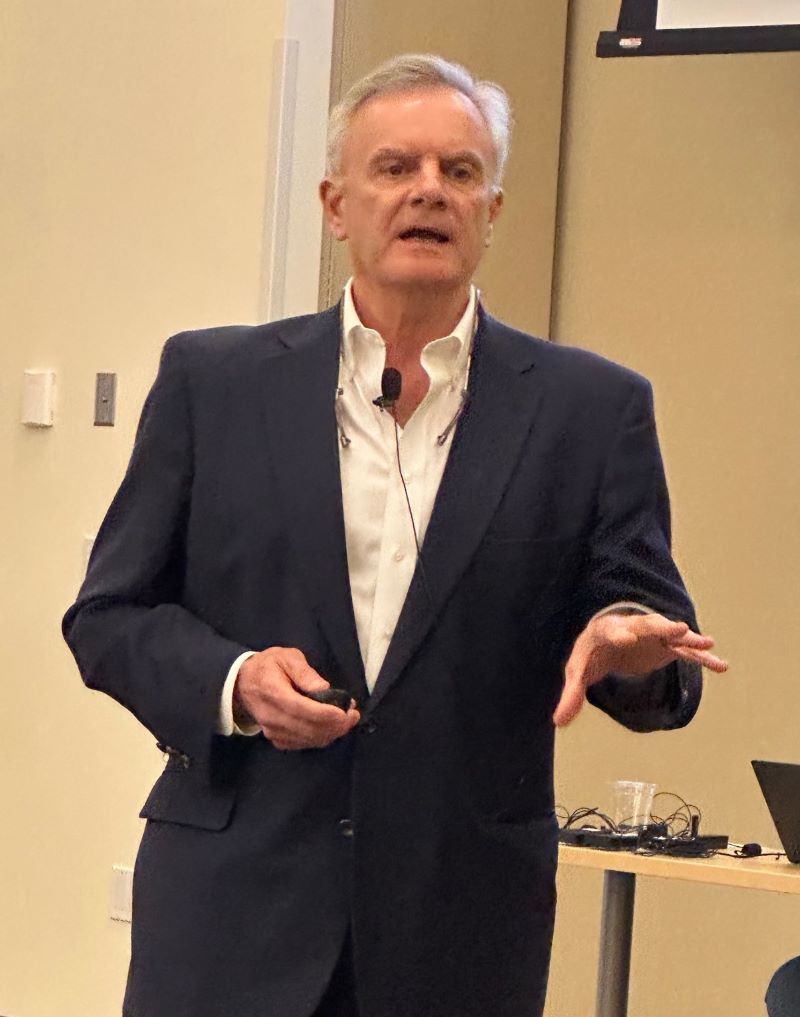
Much of the information, particularly dealing with the exemption process and the importance of various roles of both panel producers and fabricators, such as record keeping, was highly technical in nature, requiring an in-depth understanding of key metrics regarding the regulation.
It’s also why the final presentation of the day by Michael Sullivan, an attorney with Womble Bond Dickinson, was both timely and relevant.
In it he stressed the importance for every organization to have a good compliance program led by someone who can help manage and oversee such a program, delegating key tasks when necessary, but also providing a company a vision and strategy when it comes to dealing with key issues, whether it’s formaldehyde or the looming federal mandate for the stability of clothing storage units.
He began with a key question relating to these and other issues:
“How does an organization whose purpose it is to design, build and sell furniture deal with all this regulatory burden?” he said, noting that while the subject of the day was formaldehyde, there are also plenty of other regulatory issues to manage.
“The how is called a compliance program,” he said in answer to his own question. “Think about it — compliance is the internal processes and procedures that run your business. Regulations and the law are reality — how you deal with them has got to be part of how you design, build and sell furniture. There has to be a formality in your organization for managing this part of the business.”
But he said that managing compliance is not a one-size-fits-all issue. In other words, he noted, the policies and procedures in your business should be tailored to how you run your operation in dealing with the challenges.
“The single most important thing that can be done when you are considering a compliance program is to be honest with yourself,” he said. “What is my business actually like? Where are we today? What do we need to do to develop polices and procedures to comply with issues like formaldehyde regulation? And whichever tip-over regulation the world ends up with in nine months? … The beginning of a good compliance program is looking carefully and honestly at yourself and saying, ‘Here’s where we have problems, here’s where we have strengths, and how do I design my policies and procedures to get me where I need to be?’”
He said an educational component is also critical to the process, including events and workshops like the one he was speaking at as well as other in-house training.
“It’s time to start thinking about having a formalized structure not just for this emergency, but for the next one you know is going to be coming,” he said.
And having a good compliance program, he noted, starts at the top, with the president, the chief executive officer, the ownership of the company and the board, all supporting it in earnest.
Then, he said, the company has to be prepared to train its employees in the area of compliance, with the understanding that it’s going to be part of day-to-day business, whether we’re talking about the design or engineering side or customer relations.
“Because of the volume of regulations that you are seeing these days, particularly with things like international sanctions, it affects everyone’s business. It is necessary that every business have a component of compliance as part of its day-to-day operations.”
“Compliance isn’t the ugly stepchild in the corner while the rest of the pretty side of the business is over here,” he added. “The compliance program should be integrated into all of your operations. It is a collaborative effort.”
He added that having a lead compliance officer who takes ownership of the issue is important, but that it is necessary to have a team to help execute the details such as testing requirements related to things like the formaldehyde rule or even anti-tipping.
Having such collaboration, he noted, allows not only for proactive types of thinking and actions in the organization, but also a unified effort that makes handling the task a little easier.
“You will find that when you are proactive and not reactive, changes like the formaldehyde rule … are swallowed a little bit easier. You are not biting the elephant. You are just taking it one bite at a time. This is how it gets done, by a compliance program that is integrated throughout the teams in the organization.”
Other key things he noted that companies need to consider include:
+ Keeping good records. “If you don’t have a record that you did it and you can’t produce a record to show that you did it, you did not do it. … Because when something goes wrong or someone like me comes in and says, ‘Well, tell me what you did’ and you tell me and then I say, ‘Show me. Prove it to me that you did that.’ — it’s record keeping.”
+ Technology is your friend when it comes to compliance. Sullivan said that every day new and better software products are being developed to help manage all this information related to compliance and record keeping. “It can be both tailored to your business and tailored to the particular regulation you have to comply with.”
+ Be proactive, not reactive, in regards to compliance. “I want to encourage you to think about a compliance program as a proactive, not as a reactive, tool,” Sullivan said. “And having a compliance program today is going to help you catch up with what you may need to do with regard to formaldehyde. But having a compliance program in place is something that keeps you ahead, not behind. It has a lot of advantages, you don’t get surprised and at a minimum it reduces economic exposure when risk arises. That’s because the job of the compliance program is to look around the corner.”
“Don’t wait for the events to overwhelm you,” he added. “The compliance program’s job is to stay ahead. It is not just to produce the records for the audit. It is to stay ahead on what potential new sanctions are coming down the pike that will affect my ability to buy raw materials. That is what a compliance program does. It is a proactive part of your business and I would suggest an economic value-added part of your business when you look at it in that fashion.”