The company is shifting space formerly used to warehouse imported goods to boost its domestic upholstery and wood manufacturing
MORGANTON, N.C. — Luxury furniture manufacturer EJ Victor is expecting to boost its domestic capacity this year between 40% and 50% thanks to a change in use of its 200,000-square- foot production facilities here.
The company aims to accomplish this by converting space previously used to warehouse imported goods to manufacturing, which has resulted from it importing less and manufacturing more finished product in-house.
Helping fund the shift is a building reuse grant it received late last year from the State of North Carolina. The $240,000 grant, as previously reported by Home News Now, will help offset the cost of the effort.
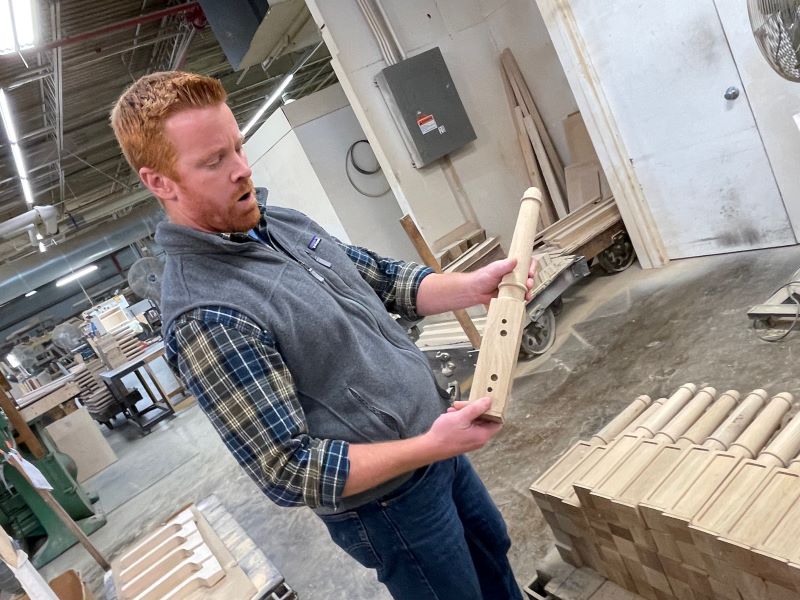
The company itself is investing some $1.6 million in the project, including about $1 million in equipment such as three-and five-axis routers, a wide belt planer sander and a combination planer to name several key pieces used in wood processing for upholstery frames and case goods.
The latest project is part of EJ Victor’s ongoing commitment to domestic manufacturing in the past five years or more. While most of its upholstery was always produced domestically, it has shifted the majority of its wood line back to the U.S. from countries such as Vietnam during that period.
The shift has resulted in more work being done in house including wood processing, assembly and finishing. The company also is creating a more vertically integrated upholstery operation by producing more wood and foam components in house.
“Just by being able to really control as much of the manufacturing process as we can internally, it has allowed us to really control our supply chain and control our processes,” David Bennett, president and CEO, told Home News Now. “Yes, it’s more complex — you have more moving parts, but you control those moving parts as opposed to having third party vendors. So from our perspective, that has been a huge game changer for us.”
Bennett recently provided an update on the project, which he said is expected to be completed sometime in the third quarter. It also is expected to create about 30 new jobs, which are in addition to the 180 the company now employs.
Bennett also noted that a big part of the investment in new production space will boost the overall output of the plant both in the short and long term. For example, within its existing building the company will add about 30,000 square feet of upholstery manufacturing and another 10,000 square feet for wood production, which includes some parts made for the upholstery side such as frames.
The additional capacity, he noted, will benefit customers in different segments it serves from designers and residential furniture retailers to private label, OEM customers and customers in the hospitality segment. On the upholstery side for example, the additional space will expand capacity by about 40%. On the wood side it is expected to boost capacity by as 50%.
“We have gone out to our existing customers as well as some potential customers and new customers to say we have some new capacity coming on line here,” he said. “We are excited about it because it gives us the ability to really utilize all we have done over the past four to five years by reshoring production. Having that successfully come to fruition has been one of those things that as a company we are all very proud of.”
EJ Victor is not the only domestic producer to make such a shift. Bassett. Va.-based Bassett Furniture, for example, has shifted some of the space it has used for warehousing imported goods to production of its solid wood BenchMade line.
Yet it hasn’t been the norm for an industry that still relies heavily on imports.
Having grown up in Morganton, Bennett has seen firsthand the shift of jobs overseas and the subsequent shift of manufacturing space to warehouse space for imported goods. For him, it is satisfying to be able to reverse that to a degree.
“We are moving in the opposite direction and taking back some of that space for domestic production,” he said.
While its not clear how much the move will reduce lead times — now about eight weeks for upholstery and 14-16 weeks on case goods not receiving any customization — he believes the additional capacity will improve the company’s speed to market over time.
“It’s definitely significant,” he said of the company’s $1 million investment in machinery alone, which is similar to what its spent on machinery in the past several years. “That’s because we really believe this is the pathway forward. We have seen that globalization has had its place, but at the same time, when the supply chain breaks down, it breaks down very fast and it takes a long time to recover. So just the fragility of that global market for us is much more of a risk than to make it here.”