Luxury furniture producer is adding workers to further reduce backlogs and lead times
HIGH POINT – Bakers Furniture’s management team has made a concerted effort over the past year to boost the utilization of the company’s upholstery plant here, bringing in more product and boosting worker hours to get that product made and shipped.
Having been operating on short time for many years prior — as low as 32 hours a week, not including some entire weeks off — the luxury furniture manufacturer boosted production to as many as 44 hours per week in early 2020.
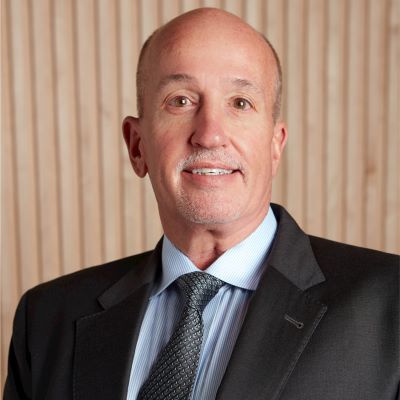
“It was under-utilized,” said Baker President and CEO Mike Jolly of the plant. “So we made a concerted effort to bring out more upholstery items and we targeted them for this facility.”
The strategy appears to have worked even better than anyone had hoped.
Due to high demand among designers and their clients, the plant has been running at around 50 hours a week in recent months for a made-to-order selection including sofas, sectionals, loveseats, chaises, ottomans, beds and chairs available in some 800-1,000 fabrics.
It’s been a good problem to have on the sales side, but a challenge on the production side as the longer-than-normal weeks are due to a high backlog estimated at around $3.9 million, or around nine weeks of production.
While that’s down from just over $5 million this past spring, or about 12-15 weeks of backlog, it’s still higher than the $2.7 million the company is trying to get by year end, according to Rick Stanco, plant manager.
“I was at $5.1 million,” Stanco said of the higher backlog this past spring when supply chain issues involving foam and other materials began to surface. “So we said “let’s see if we can get to the fours and then if we can get into the threes.” We got to 3.7 (weeks in late October), so we were heading in the right direction.”
Sales have boosted the backlog up to nearly $4 million in recent weeks, which has had the plant running nine hours a day Monday through Thursday, eight on Friday and six on Saturday.
While Stanco is still hoping to lower backlogs – the rough equivalent of lead times – even further, it will take another nine to 10 workers, which would bring the payroll to just over 60 production workers in High Point.
“We are obviously trying to add on people because we don’t want them to stay on this type of shift, and the flow is not going to go down,” Jolly said of the need for additional workers. “We need to get back to 42-44 hours.”
Jolly noted that Baker is still doing a lot better in terms of lead times compared to some upper end competitors, which sell some product in dedicated Baker showrooms. For some of those companies, which officials declined to name, the lead times are out to 28 weeks, Jolly said.
Achieving a lower backlog than some hasn’t been easy. But the company said that its success was due in part to some key factors including having maintained strong relationships with key vendors.
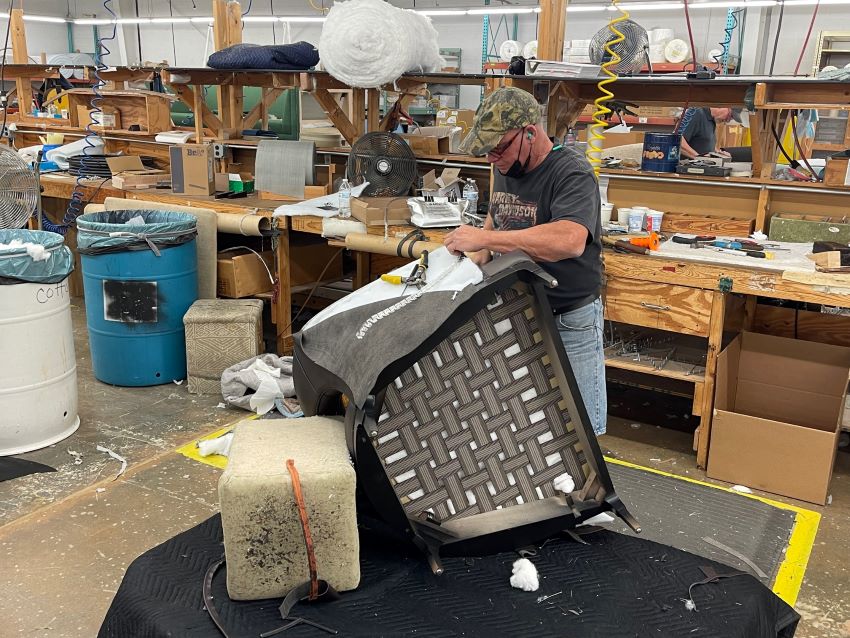
“It didn’t last long for us,” Jolly said of the foam shortages. “And it hit later for us. Because we deal with very small vendors – they basically have been doing our cushions forever and it’s a partnership – it is very customized in terms of the feel and the comfort of the cushions because we are not buying them from four or five different places. It did (drive up the backlog) during that time but they continued to spoon feed us as much as they could.”
The company also worked shorter weeks than normal before the supply situation – including the availability of plywood – gradually improved.
“We kept struggling along is what we did during that time, although we weren’t working full weeks… We got back on our feet fairly quickly,” Jolly said. “Some companies are still reeling from it.”
And during what normally would have been an early July slowdown, the company found it had enough materials to keep the plant running at full — if not higher than normal capacity.
“Then we started to put the pedal to the metal,” Jolly said, realizing the company was in an enviable position in terms of both sales and its materials inventory, including some 140 fabrics it tries to keep in stock at all times. “We kept adding hours based on the materials that we had on hand. Now we have a backlog of materials in stock.”
“We are at the point now where we can get all that we need,” Stanco added.
Now if the company could only get those nine or so additional workers it needs by year end. It’s a challenge given that many don’t like to change jobs right before the holidays fearing they will lose out on a year-end bonus or some unused vacation time.
But Stanco said the company is taking steps to fill the jobs as quickly as possible moving trimmers into the upholstery slots as trimmer jobs are often easier to fill. The process, he added, is still slow, with interviews taking place one at a time.
But as each of those job seekers come into the fold, the company is getting one step closer to having the full team it needs to get its lead times and work schedules back in line with where the company wants them to be.