ST. PETERSBURG, Fla. — When I heard about a micro-factory in St. Petersburg, Florida, deploying AI-powered 3D printing to make furniture, I knew I needed to find out more. The business model is just so sexy. Take waste materials, melt them down into granules, then feed those granules to an army of AI-powered, Transformerlike robots that can take a CAD file and 3D print just about whatever you like.
The company is HADDY, an acronym for Heroic Agile Design Durable Yours, which sounds like AI came up with it. But, last month HADDY moved into a 32,000-square-foot factory in St. Pete’s hip, colorful Edge District. I submitted a press inquiry but haven’t yet heard back, so most of what I learned I picked up from the HADDY website and local news reporting.
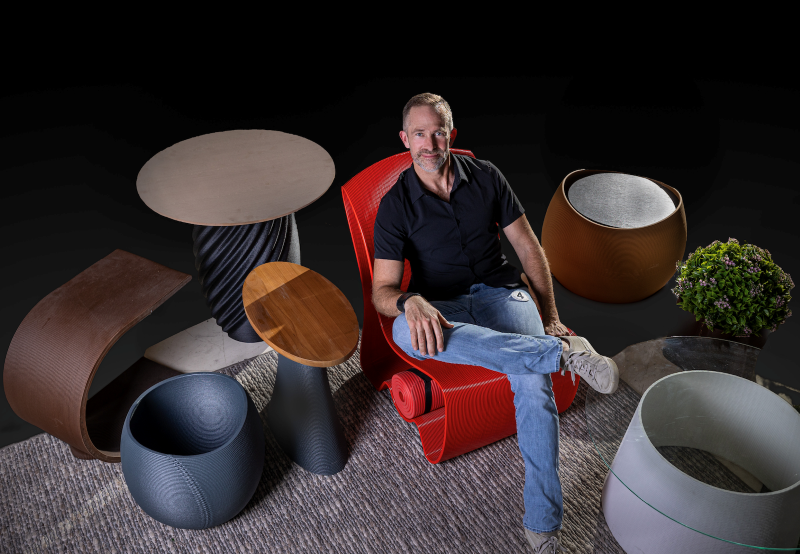
According to St. Pete Rising, HADDY is 3D printing chairs, tubs, tables, planters and even an entire coffee bar, to name just a few objects, all of them from melted-down fishing nets and discarded plastics such as water bottles. The plan is to open up micro-factories like the one in St. Pete all over the world, starting with seven in the next few years, according to founding CEO Jay Rogers, speaking at HADDY’s grand opening last month. Micro-factories are slated for “major metropolitan cities” in the U.S., including the Midwest and West Coast, and for international markets.
Rogers is a veteran of the Marine Corps, and he’s a Guinness world record holder for 3D printing a functional electric car. I’ll come back to that later.
In my query to HADDY, I asked about the distribution model. Rogers told St. Pete Rising that the company has “secured deals with major retailers and independent buyers,” and I found images of products on floors at Room & Board and Gardner White. I also asked for some basic information regarding price points, so if I get that I’ll pass it along.
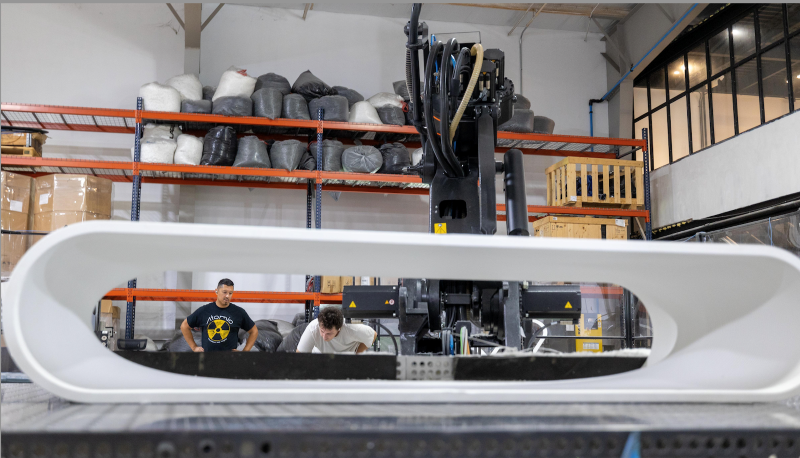
Fibonacci spiral
The secret sauce here is the six AI-powered robots, which HADDY has identified with pet names: Ada, Bumblebee, Clio, Dali, Edison and Fibonacci. My guesses here are that these names represent computer programming (Ada Lovelace was perhaps the first computer programmer), a nod to the Transformers (Bumblebee), history (Clio is the Greek muse of history), art (Dali, the surrealist painter), electricity (Edison) and math (Fibonacci).
The AI means that the robots can learn from their own actions and, therefore, become ever smarter, according to Rogers, who directs a team of actual humans who do the designing, engineering and programming. This human-robotics combo is already producing an average of about 700 objects per week, Rogers told Tampa Magazine, and if the machines are getting smarter, prices might actually come down.

The advantages here are compelling: No tariffs. No employee smoke breaks or sick days. Sustainable raw materials. A recyclable product line that can just be melted down into granules again. A supply chain that is exquisitely manageable and even controlled. A business model replicable virtually anywhere there is plenty of electricity. A costing structure presumably visible to the penny paired with production cycles likely predictable to the minute. And I would say near-zero emissions, but we are learning that the environmental cost of powering AI is anything but sustainable.
HADDY’s own literature describes the business as a “pioneering company redefining large-scale digital manufacturing.” The St. Pete micro-factory is “the largest and most powerful 3D printing facility in the world.”
Rogers said that Haddy’s new facility represents “one of the most significant leaps forward for the ‘re-industrialization’ movement in the United States. Emerging tech is paving the way. Hard-to-make products can be re-shored to regions all over the United States and made even better than when they were concentrated in low-labor locations abroad.”
Contemporary decor
Given 3D printing’s dizzying dexterity with respect to what kinds of objects it can produce, furniture is only one product category of many for HADDY. According to its own literature, on the boards are “high-impact sectors like national defense, disaster recovery, construction,” including battlefield-ready gear, modular housing components and mobile infrastructure.”
“This is America planting a flag in the future of making things,” said Lex Keifhaber, COO of the company, at the micro-factory opening. “We can build smarter, faster and cheaper, while improving overall quality. And we can do it right here at home. If you time-traveled to this moment you’d think this was insane, but it’s real.”
Now, I know you’re interested in that 3D car. Well, before Rogers partnered with venture capital firms to start up HADDY, he founded Local Motors in Phoenix, and there in 2014 he produced the world’s first 3D-printed car. Called the “Strati,” the electric car required but 44 hours to make, according to Rogers, speaking with Tampa Magazine. Before that, Local Motors rolled out the Rally, which the company said was the world’s first open source-designed race car. In 2016, Local followed up the Strati and Rally with the Olli, an open source-designed, autonomous electric bus that I remember seeing news accounts about at the time.
Important to understanding the potential of HADDY is the fact that at its peak, Local Motors had five micro-factories. In addition to the home base in Phoenix, the company opened up production facilities in Knoxville, Tennesee; Las Vegas; Louisville, Kentucky; and Washington, D.C. Also important to understanding the potential of HADDY is the rather ignominious end to Local, which shut down in 2022. After securing $1 billion in backing for the Olli and securing commitments from municipalities such as the city of Toronto, the Olli never made it onto city streets other than for testing, as far as I can tell. Poof! Gone.
By the time Local shuttered, Rogers had transitioned to an advisory role, but that end came only months after Vikrant Aggarwal had replaced Rogers as CEO, according to TechCrunch.
Reverse engineering
However, Rogers has again persuaded the venture capital community that he has an idea worth investing in and getting behind in a big way. And this time it’s an idea that the home furnishings sector could significantly benefit from, perhaps even need, because rather than the typical model of venture capital being used to hollow out furniture companies before dumping them in bankruptcy, the HADDY model takes a bunch of nothing (recyclables) and turns it into stuff we can use.
Hey, Masco! Interco! Furniture Brands International! Franchise Group! Who’s your Haddy?