Initiatives include a new plant in Vietnam, an expanded plant in India and a major new headquarters and distribution center that opened last fall in Whitsett, North Carolina
WHITSETT, N.C. — Since new ownership took the reins of furniture, lighting and accessories specialist John-Richard in 2020, the company has been involved in a growth plan to carry the business forward over the next few decades.
Of course, a global pandemic slowed the plan down as demand soared, keeping its facilities running at a record pace to fill customer orders.
But now, headed into its fifth year since the acquisition, the company has achieved major goals set forth during the shift in ownership.
These include the opening of a 250,000-square-foot furniture production plant in Vietnam last year that replaced a former 90,000-square foot facility and an expansion of its manufacturing facility in India expected to be completed in another few months. This expansion is adding about 10,000 square feet to the 30,000-square-foot operation, which produces lamps, accessories and metal accent furniture.
Last fall, the company also moved its headquarters and distribution to Whitsett after being based in Greenwood, Mississippi, for more than 40 years. In Greenwood, the company continues to operate a 250,000-square-foot plant that produces its art and botanical lines. Those products are either distributed directly to customers from that facility or consolidated with shipments from Whitsett.
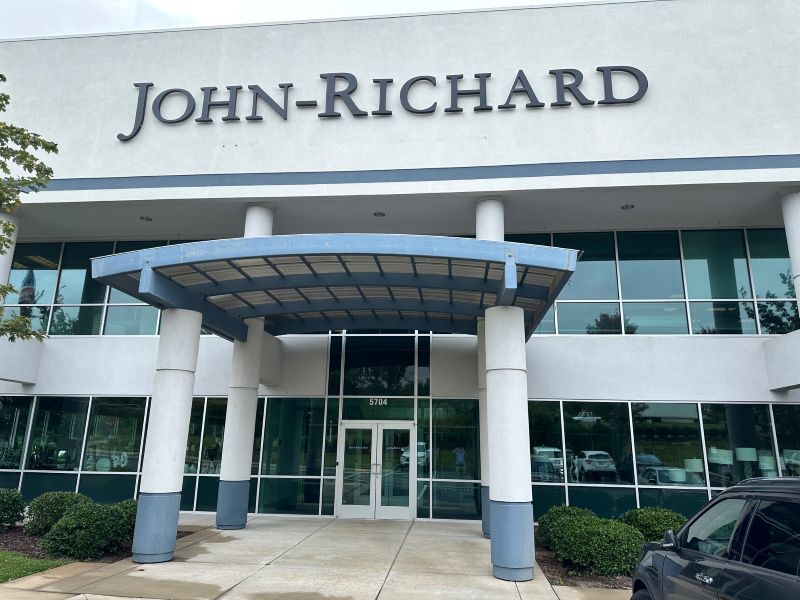
Late this past summer, Home News Now visited the company’s new 236,000-square-foot headquarters and distribution center in Whitsett to learn more about the company’s operations and how it is benefiting its many customers, both brick -and-mortar retailers and the design trade alike.
About 20,000 square feet of the facility — representing about 10,000 square feet on two floors — accommodates administrative operations, including offices for executive staff, as well as IT, product development, customer service and finance team members. It also has a photo studio and a close-out showroom for lighting, accents and other décor.
But the bulk of the facility is its warehouse and distribution center, which has about 50 dock doors for shipping and receiving product. It also has a new rack system that houses product across its lines ranging from furniture and accents to lighting, mirrors and other home décor, much of which is produced in its new Vietnam plant.
Combined with its administrative operations, the Whitsett facility is a center of operations, representing not only where the company is managed, but also where product is developed, customers are serviced and also a central location from which to flow product.
The move last fall was merely the start of a transition into the new building that involved hiring and training new workers. While the area has a lot of skilled talent, many new employees have had to learn the company’s processes and diverse product line in order to perform their respective tasks with proficiency and ease.
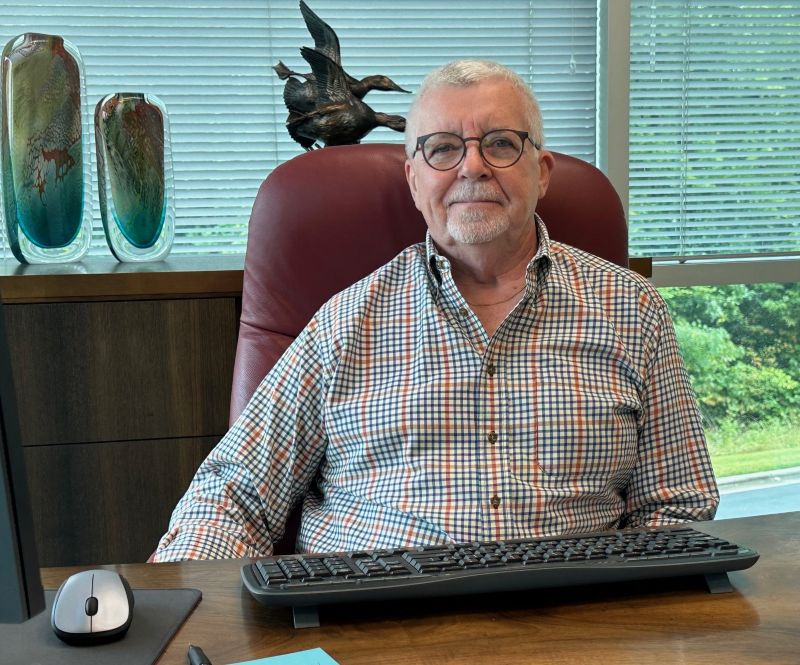
“We all know exactly how to handle this particular product out of Greenwood,” said President and CEO Alan Galbraith, who is also an owner in the business. “Then we had to hire a bunch of new people here, and even if they are experienced in the furniture business, they may not have handled our types of products before. And as a consequence, there are all these little nuances, like ‘Wait a minute, this accessory is made up of two boxes. There is a base and there is a body. … And unless someone is really paying attention, it can get messed up.’”
The process also has involved installing a vertical racking system that holds many different types of product in assigned areas, allowing it to flow efficiently in and out of the building.
A new enterprise resource planning system also allows the company to communicate between both Whitsett and Greenwood, effectively managing both operations as they each remain an integral part of the organization.
Galbraith said the implementation of the ERP system also has forced the company to write down and document specific processes, which allows different tasks to be handled consistently, ranging from how individual products are handled to how customer service reps are trained to field and answer questions about specific products.
While the early months of the transition, including implementing the ERP, was not easy by any means, Galbraith said that the operation is running a lot more smoothly.

“In the last couple of months, now, in August and September, things really calmed down and are much more predictable,” he said. “In other words, we were kind of going up and down with our shipments, again, because of the complexities of pulling together complex orders to ship to our clients. Now they have mastered that.”
He said the new facility has been good for the company and its customers in several key ways. For one, it puts the company in the heart of an area where there is a lot of industry talent. That has helped in recruiting people to work in different areas ranging from management to marketing and product development, for example.
“We benefit from all of that,” he said, adding that its customers also benefit from the standpoint that the facility has access to major highways and distribution network in the Carolinas in general, including trucking companies that specialize in furniture.
By comparison, he noted, in Greenwood, it was sometimes difficult to get carriers to come and deliver and pick up freight as it was two hours south of Memphis, Tennessee, and two hours north of Jackson, Mississippi.
“So when trucks were going cross country, they didn’t want to make a two-hour detour to pick things up,” he noted, adding that products being shipped on common carriers would go through “quite a few distribution hubs and were being handled more often than they needed to be. Whereas here, customers are going to get it directly now on these furniture carriers that we are using to distribute.”
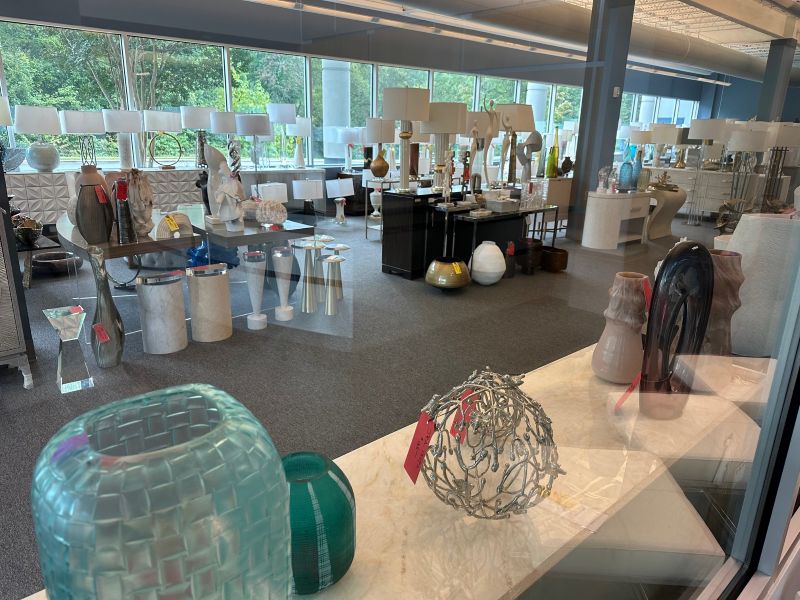
He added that this also will cut down on shipping costs for customers.
“It varies depending on where people are, but even shipping to the West Coast, there are advantages to being in the Carolinas,” he said. “There are a lot of advantages for our customers.”
Most importantly, the new headquarters and distribution center, combined with its new manufacturing operations in Vietnam and India, have positioned the company for growth now and in the future.
“Things have really smoothed out, and I have high hopes,” Galbraith said, noting that while Covid slowed down some of the growth plans, the timing worked out well, particularly in light of the opportunities that are starting to arise, particularly with an improved housing market and economy in general anticipated for next year and beyond. “Here we are coming up on our fifth anniversary. We have done an awful lot in five years. And we are looking forward to the future for sure.”